2節 表面処理
14.2.1 ステンレスの表面仕上げ
(1) ステンレスの一般的な表面仕上げを表14.2.1に示す。
表14.2.1 ステンレス板の表面仕上げ(その1)
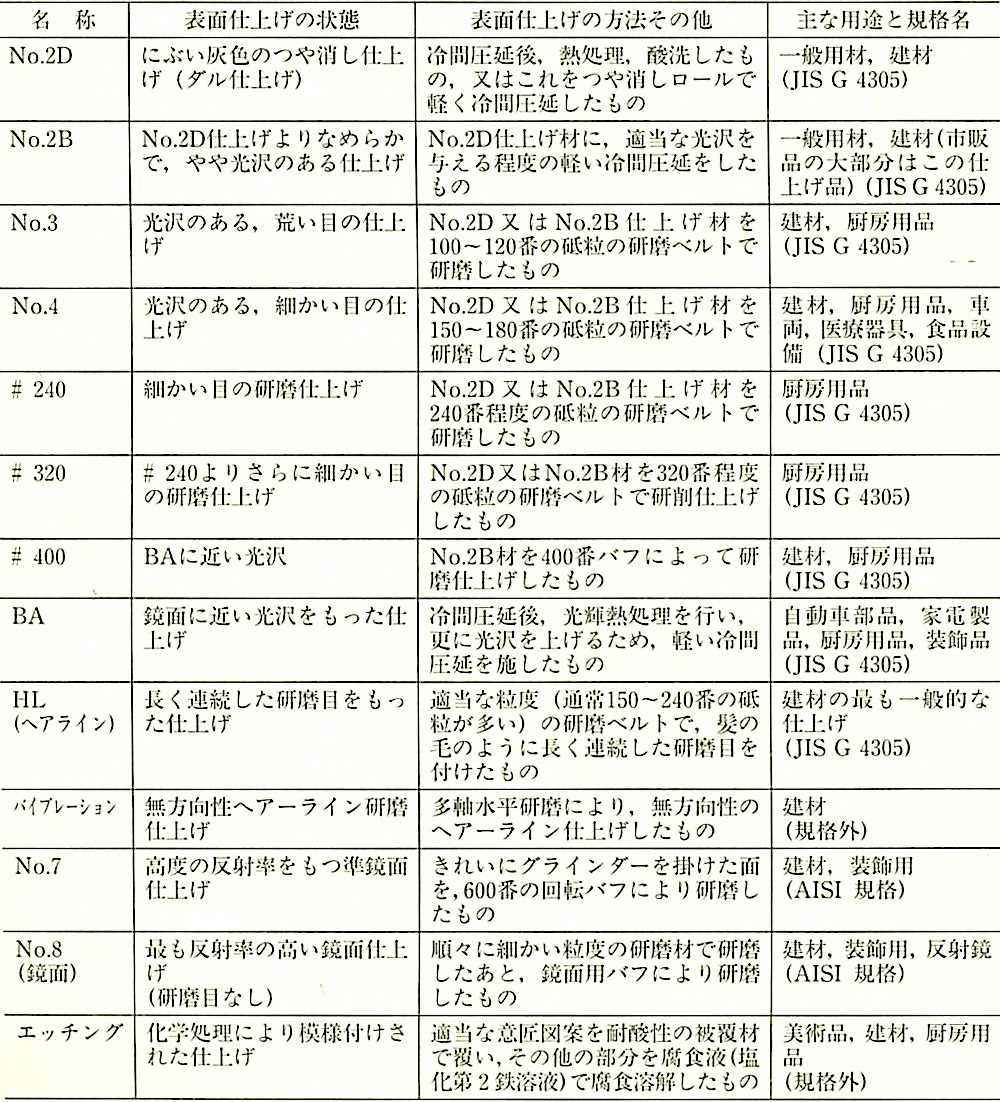
表14.2.1 ステンレス板の表面仕上げ(その2)
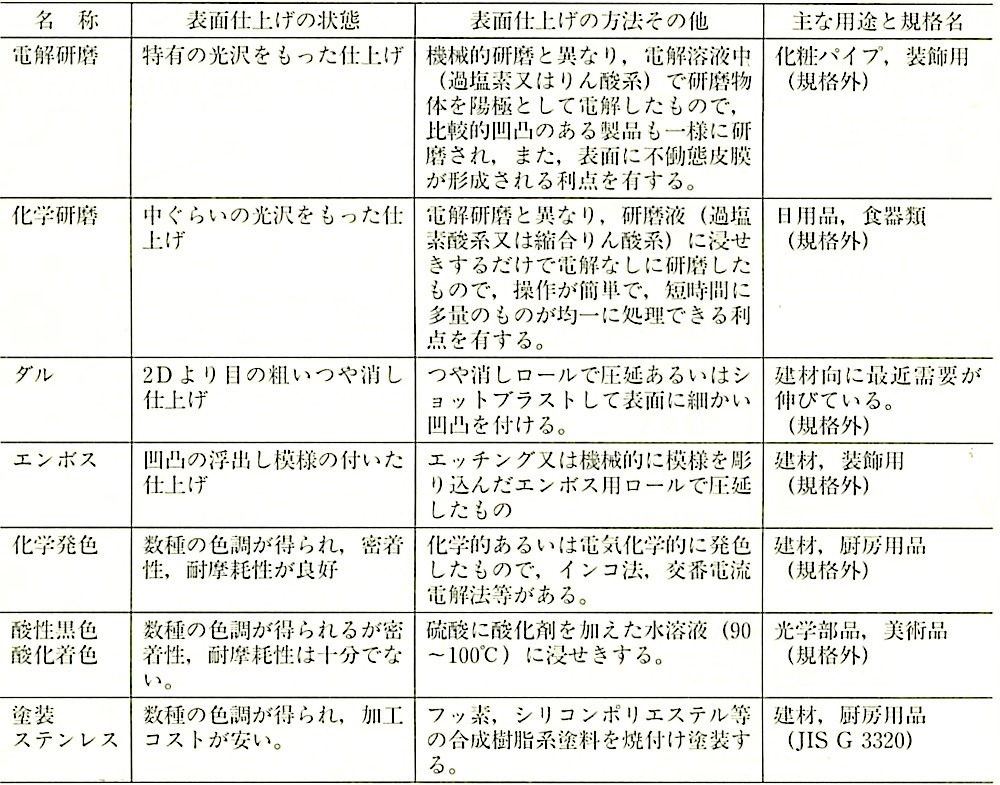
(2) ステンレスの表面仕上げで表14.2.1以外には、めっき(金、銅、アルミ)、ドライコーティング等があるが、これらは、製作所が限定される。
(b) 建築材料としては、反射率の高いものは嫌われる領向にあるが、耐食性ではこの方が優れている。屋根等の防眩性が必要な部位については、防眩性に優れたダル仕上げを選定することがある。
表面を荒らすと大気中のほこり等がたまりやすく、腐食の原因になりやすい。しかし、「標仕」14.2.1では、美観を重視し、板材に限らずステンレスの表面仕上げは、指定がなければJIS G 4305(冷間圧延ステンレス鋼板及び鋼幣)のHL仕上げ程度と定められている。
なお、「標仕」でいう軽易な場合とはフード等である。
(c) 一般にヘアライン仕上げという場合は、HL仕上げのことをいう。この仕上げは、加工後生じた傷や溶接部分等に対し容易に補修ができるが、錆等がつきやすい。
その他の仕上げについては、加工後の傷の補修が困難であり、使用に当たっては、その点を考慮しなくてはならない。
14.2.2 アルミニウム及びアルミニウム合金の表面処理
(a) 表面処理の分類
アルミニウム表面処理の種類及び種別は図14.2.1に示すとおりである。また、これらの処理に意匠的な仕上げとして、研磨、エッチング、染色等の処理も行われることがある。
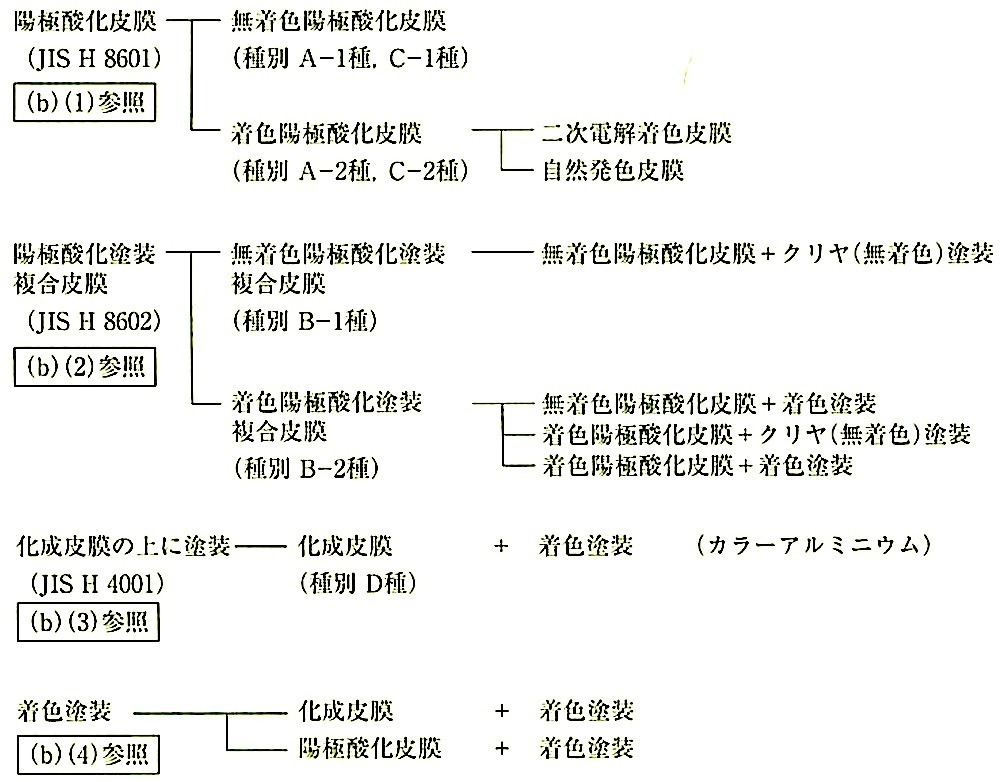
図14.2.1 アルミニウム表面処理の種類及び種別
(b) 各種表面処理の概要
(1) 陽極酸化皮膜
アルミニウムを陽極として、硫酸、その他の電解液で電気分解すると、表面にち密な酸化皮膜を生成し、耐食性、耐摩耗性を向上させることができる。この皮膜を模型図で示すと図14.2.2のようになっており、多数の微細孔がある。この微細孔に金属等を析出させ、容易に着色させることができる。また、この微細孔は封鎖する必要があり、一般に沸騰水等で処理し酸化皮膜が沸騰水との反応により水和化合物を生成し、不活性化すると同時に体積膨張等により封鎖する。これを水和封孔処理という。
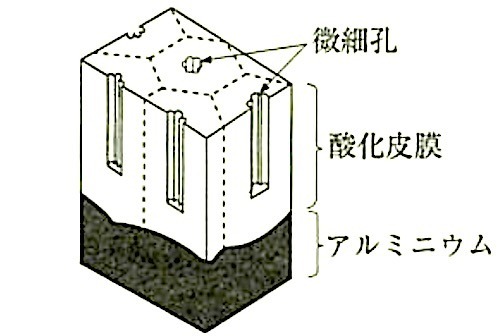
図14.2.2 陽極酸化皮膜の模型図
なお、水和封孔処理された酸化皮膜は大気中に暴露されたのちも不活性状態が保持され優れた耐食性及び耐汚染性を示す。
JIS H 8601(アルミニウム及びアルミニウム合金の陽極酸化皮膜)では、皮膜厚さの種類と耐食性、耐摩耗性及び封孔度について規定している。
(i) 無着色陽極酸化皮膜
陽極酸化皮膜及び封孔処理を行い、着色や染色を行わないでアルミニウム素地のシルバ一色のままを無着色仕上げとするもので、「標仕」表14.2.1では皮膜の種類(厚さ)により、A-1種、C-1種として規定している。
(ii) 着色陽極酸化皮膜
着色傷極酸化皮膜は、「標仕」表14.2.1では皮膜の厚さにより、A-2種、C-2種を規定している。
なお、着色方法には、次の種類がある。
?@ 二次電解着色皮膜
二次電解着色とは、陽極酸化処理後、金属塩類を含む電解液中で二次的な電解処理により、皮膜の微細孔中に金属を析出することにより着色(ゴールドアンバー、ブロンズ.プラック等)する方法である。
なお、「標仕」14.2.2(b)では、特記がなければ、着色方法は、二次電解着色としている。
?A 自然発色皮膜
自然発色皮膜には、素材中の合金成分を皮膜中に残存させ発色させる合金発色法、電解液に有機酸を用いて皮膜を発色させる電解発色法及びこれらを組み合わせて発色させる方法がある。
(2) 陽極酸化塗装複合皮膜
陽極酸化塗装複合皮膜は、アルミニウムに平均皮膜厚さ 5μm以上の陽極酸化処理を施したのち、塗装を施すことによって陽極酸化皮膜の性能に塗膜の性能を付加して、耐食性、耐候性、装飾性等の品質を更に向上させた皮膜であり、アルミニウム建材の表面処理で主流となっている。
JIS H 8602(アルミニウム及びアルミニウム合金の陽極酸化塗装複合皮膜)は、2010年1月に改正されており、従来の皮膜厚さ及び塗膜厚さを規定した仕様規定から、用途及び適用環境により要求される特性項目とその合格基準を定める性能規定に変更された。この規格では複合皮膜の種類を複合耐食性及び耐候性により「A1、A2、B、C」の4種類に区分し、その品質を定めている。
「標仕」表14.2.1では、無着色陽極酸化塗装複合皮膜を「種別 B-1種」、着色陽極酸化塗装複合皮膜を「種別 B-2種」と規定しており、これに対応するJISの種類は「B(一般的な環境の屋外)」としている。しかし、使用する環境によっては、表14.2.3により適切な種類のものが選定される。
なお、改正JISの「種類B」は内容が変更されており、表C.1のように「旧種類B (透明系塗膜)」と「旧種類P(着色系塗膜)」の両方が含まれる形となって いる。したがって、これまで「標仕」では、「B-1種」は陽極酸化皮膜が無着色のもの、「B-2種」は皮膜が着色されたものとしていたが、JISの改正により、図14.2.1のように「B-1種」は陽極酸化皮膜及び塗膜のいずれも無着色のもの、「B-2種」は陽極酸化皮膜及び塗膜のいずれか又は両方が着色されたものとなっている。
塗装方法については、工場で行う主なものとして、電解塗装及び静電塗装がある。
(3) 化成皮膜の上に塗装(JIS H 4001による塗装)
アルミニウム及びアルミニウム合金の焼付け塗装板及び条(通称、カラーアルミ)の製品については、JIS H 4001(アルミニウム及びアルミニウム合金の焼付け塗装板及び条)が定められており、JIS H 4001では、種類及び記号(原板による区分、色による区分、つやによる区分)、品質(外観、膜厚、鉛筆引っかき硬度、付着性、耐曲げ性、耐おもり落下性、耐塩水噴霧性、耐候性、耐酸性及び耐アルカリ性、耐湿性)、寸法及び寸法許容差、質別及び機械的性質、試験及び検査等について規定されている。
「標仕」表14.2.1のD種の表面処理では、JIS H 4001における塗装が規定されている。塗装方法としては、通常、化成皮膜処理を施した上にロールコータ塗装である。
(4) 着色塗膜
「標仕」表14.2.1に規定する A〜D種以外の表面処理の種類としてアルミニウム製カーテンウォール等に用いられる着色塗膜がある。
アルミニウムは、そのままでは塗料の付着性が良くないので通常下地処理として化成皮膜又は陽極酸化皮膜が施される。下地皮膜は、それ自体による防食性よりも、その上に施される塗膜との適合性が大切であり、塗膜の付着性をはじめとする種々の性能を考慮し、下地を選択する必要がある。
着色塗膜に使用する塗料の種類としてアクリル樹脂系、ポリエステル樹脂系、ポリウレタン樹脂系、アクリルシリコン樹脂系、ふっ素樹脂系等のものがあり、一般にはアクリル樹脂系やポリウレタン樹脂系の塗料が使用される。より耐候性が要求される環境で使用される場合は、ふっ素樹脂系塗料が施される。
塗膜の厚さは 20〜50μm程度であるが、色の均一性、隠ぺい性、使用環境や耐久性等を考慮して定める必要がある。また、塗装方法は、静電塗装、吹付塗装で行われる。
(5) 塗装に関する説明
(2)、(3)及び(4)の具体的な塗装方法については次のとおりである。
?@ 下地処理
1) 化成皮膜処理
酸性の水溶液中に浸せき処理し、アルミニウム表面に酸化皮膜、クロム酸塩皮膜、りん酸・クロム酸塩皮膜等を生成させる方法である。
皮膜は、陽極酸化皮膜より極めて薄く,柔らかいもので、耐食性を必要とするところにはそのままでは使用できない。
また、着色も不均ーであるため装飾用には不適当である。したがって、アルミニウムと塗料との密着性を増加させるため、塗装下地処理として使用される。「標仕」表14.2.1で規定しているD種は、化成皮膜の上に着色塗装を施したものである。
処理方法の一例を表14.2.2に示す。
表14.2.2 化成皮膜処理方法の特徴
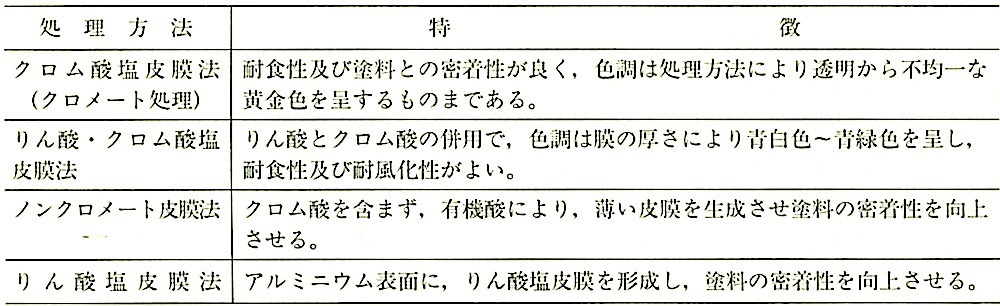
2) 陽極酸化皮膜
塗装下地としての陽極酸化皮膜は、(1)の陽極酸化皮膜と同様であるが、それ自体の性能よりも塗膜の性能を安定して付与する目的から皮膜厚さ等の規定はない。
?A 塗装方法
1) 電装塗装
電気泳動法によって塗装する方法である。水溶性塗料中で被塗物を陽極として、直流電流を用いて塗装する方法であり、複雑な形状のものでも比較的均ーな膜厚が得られる。
2) 静電塗装
塗装損失が少なく高能率の塗装法として広く採用されている。被塗物(陽極)と塗料のノズル(陰極)の間に60,000〜100,000Vの直流電圧をかけ、帯電した塗料粒子を付着させる。静電塗装には形状、霧化方式により多くの種類がある。
3) 吹付け塗装
塗料をスプレーガンで吹き付ける方法であり、常温又は加熱塗料( 70〜80℃)を空気圧で霧化する方法と、塗料自体に高圧をかけその膨張により霧化するエアレス塗装の2種類がある。
4) ロールコータ塗装
金属平板やコイル塗装に適用され、ナチュラル形とリバース形がある。前者は17μm以下の薄膜塗装、後者は20μm以上の膜厚塗装に適する。
5) 粉体塗装
溶剤や水等の溶媒を含まないで粉体塗料粒子を被塗物に付着させる方法である。一般に他の塗装方法に比べて厚膜になる。
?B 乾燥及び焼付け条件
乾燥及び焼付け条件は、使用する塗料の種類により異なり、通常工場塗装ではポリウレタン樹脂系塗料は100℃ × 30分間、アクリル樹脂系塗料は180℃ × 30分間、ふっ素樹脂系塗料では低温型:100℃ × 30分間、中温型:160℃ × 30分間、高温型:230℃ × 20分間が標準とされている。
(c) 「標仕」表14.2.1のアルミニウム及びアルミニウム合金の表面処理の種別による適用は、次のようなものを想定している。
(1) A – 1、2種はメタルカーテンウォール等
(2) B – 1、2種は一般アルミサッシ、外装材等
(3) C – 1、2種はカーテンボックス等建物内部に使用する内装材
(4) D種は建物内部に使用する成形板及び屋根材
上記のうち、A種、C種は陽極酸化皮膜のままのため「標仕」14.2.2(c)(1)では、アルカリ材料と接する箇所は耐アルカリ性の塗料を塗布すると規定している。
また、シーリング接着面については、水和封孔処理を施した表面には生成物が付着していることがあるため「標仕」14.2.2(c)(2)では、この生成物を取り除くこととしている。塗装品についても、シーリング材との接着性を確認のうえ、選定することが必要である。
なお、「標仕」表14.2.1では種別が示されているが、これは一般的な斑対iの屋外や屋内に適用されるものであり、海浜や沿岸等腐食・劣化の激しい環境や過酷な条件で使用する場合には、耐久性向上のため皮膜等級や複合皮膜の種類が高いものを使用する必要がある。
(d) 陽極酸化皮膜の性能
陽極酸化皮膜の性能については、JIS H 8601(アルミニウム及びアルミニウム合金の陽極酸化皮膜)に規定されており、その抜粋を次に示す。
JISでは、使用環境別試験の項目を規定しており、一般的な建築部材の場合、外観、皮膜厚さ、キャス耐食性、耐摩耗性が規定されている。
なお、JIS規格中の各試験方法については、(g)による。
6. 特性及び品質
皮膜の特性及び品牲については、6.1から6.12に示す。このうち、適用される製品に必要な特性及び品質は、用途を考慮して取り決めるものとするが、一般に広く必要とされる重要な特性と用途を表1に示す。
なお、受渡当事者間による特別な協定がなされていない限り、表1の使用環境別試験項目及び各品質項目の規定を適用する。その他の品質項目については、特別な用途についてだけ要求される場合があり、必要に応じて受渡当事者間の協定で取り決めるものとする。試験は、7.に規定する試験方法によって行う。( 6.の一部及び 7.は省略)
表1 使用環境別試験項目
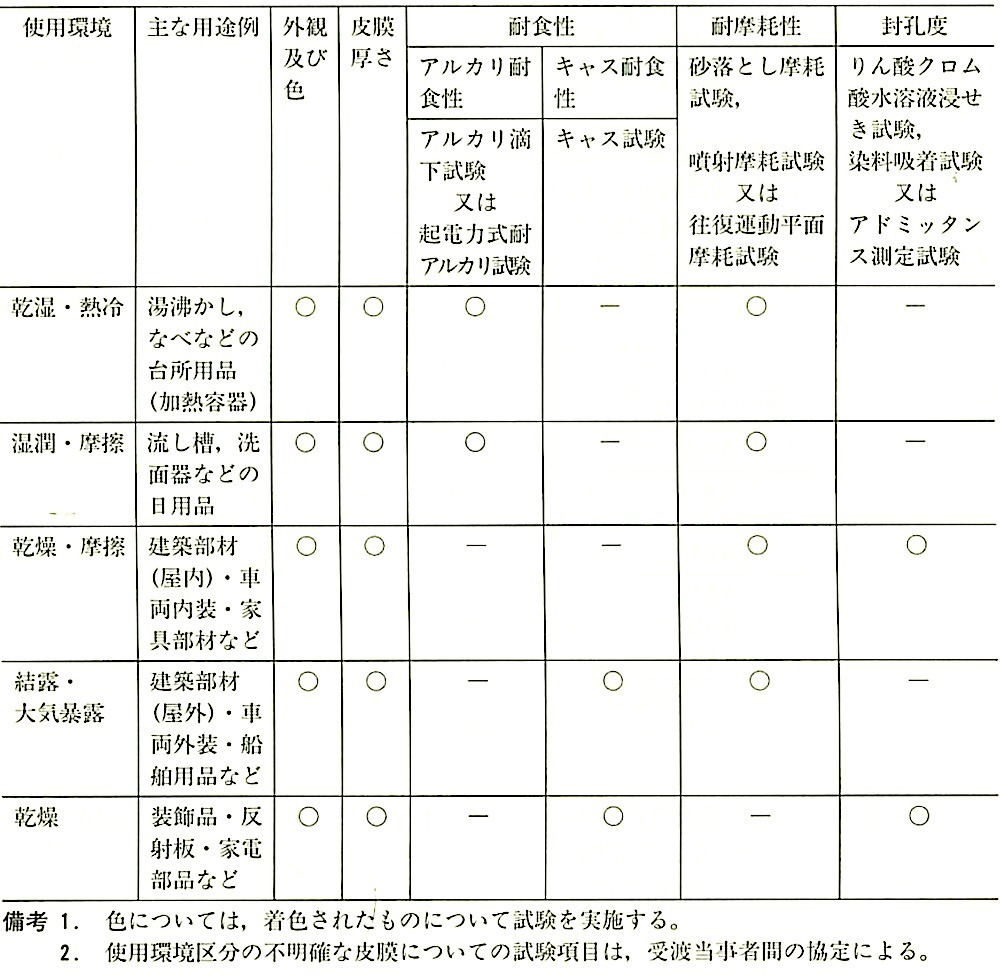
6.1 外観及び色
6.1.1 外観
皮膜の外観は、有効面上に、きず、表面上のむら、粉ふきなどの用途上有害な欠陥がないものとする。外観の品質は、必要に応じて受渡当事者間で合意した標準見本又は限度見本によって行ってもよい。
6.1.2 色とその許容範囲
色とその許容範囲は、受渡当時者間の協定によって取り決める。色とその許容範囲の品質は、必要に応じて受渡当事者間で合意した標準見本又は限度見本によって行ってもよい。
6.2 皮膜厚さ
6.2.1 皮膜厚さの等級
皮膜厚さは.平均皮膜厚さ(μm)によって表し、表2に適合しなければならない。
なお、皮膜厚さの等級は、製品の用途及び使用環境などを考慮して選択するが、受渡当事者間で特別な協定がない限り、表2による。
表2 皮膜厚さの等級

6.2.2 皮膜厚さの等級と主な用途例
皮膜厚さの等級は、製品の用途及び使用環境を考慮して選択するが、受渡当事者llりで特別な協定がない限り、表3による。
なお、用途によって特別な皮膜厚さが要求される場合は、表2に規定する平均皮膜厚さの等級にない平均皮膜厚さを決めてもよい。
表3 皮膜厚さの等級と主な用途例
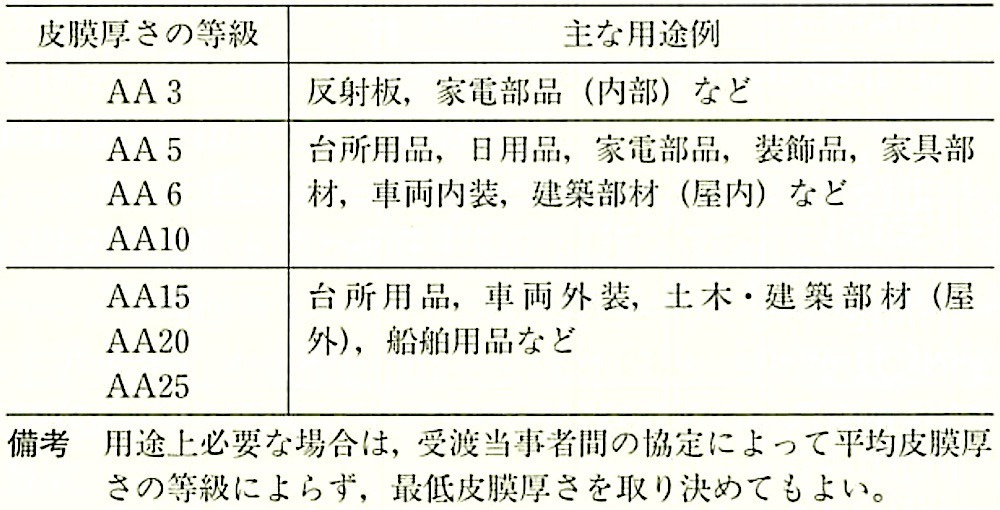
6.3 耐食性
皮膜の耐食性は、各種の環境に耐える特性で、用途によっては酸性、アルカリ性及び塩水雰囲気などの環境に耐える特性が要求される場合があるが、その品質は表 4又は表5に適合しなければならない。
表4 アルカリ耐食性
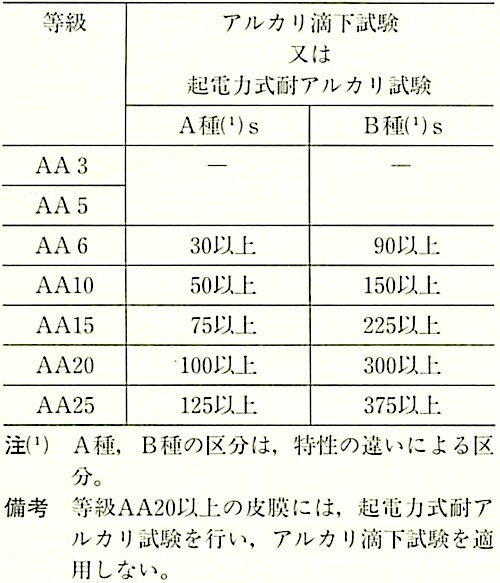
表5 キャス耐食性
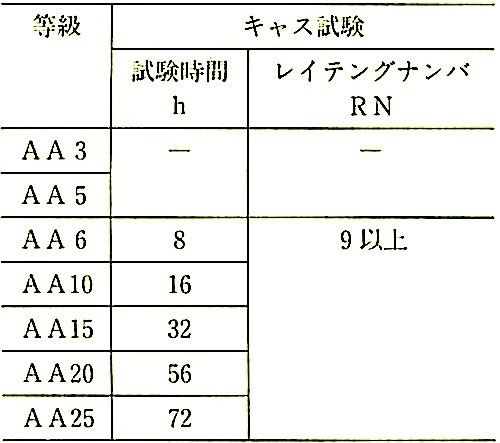
6.4 耐摩耗性
皮膜の耐摩耗性は、摩耗環境に耐える特性であり、用途によっては摩耗性物質の衝突による摩耗、しゅう(摺)動摩耗及び転がり摩擦などの摩耗環境に耐える特性が要求される場合が、あるがその品質は表6のいずれかに適合しなければならない。
なお、噴射摩耗試験の耐摩耗性は、導通判定法によることとし、素地が露出するまでの摩耗時間 [ W J (T)]で表す。
表6 耐摩耗性
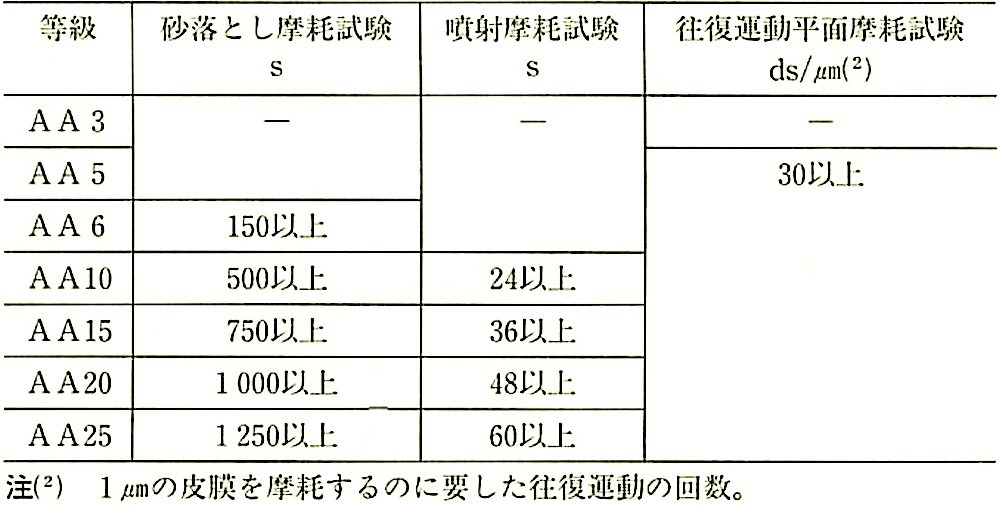
6.5 封孔度
封孔度は、各種環境に適用した場合の耐食性、耐汚染性などを左右する重要な特性であり、特別な用途として封孔しない皮膜が要求される場合及び AA3を除き、表7のいずれかに適合しなければならない。
表7 封孔度
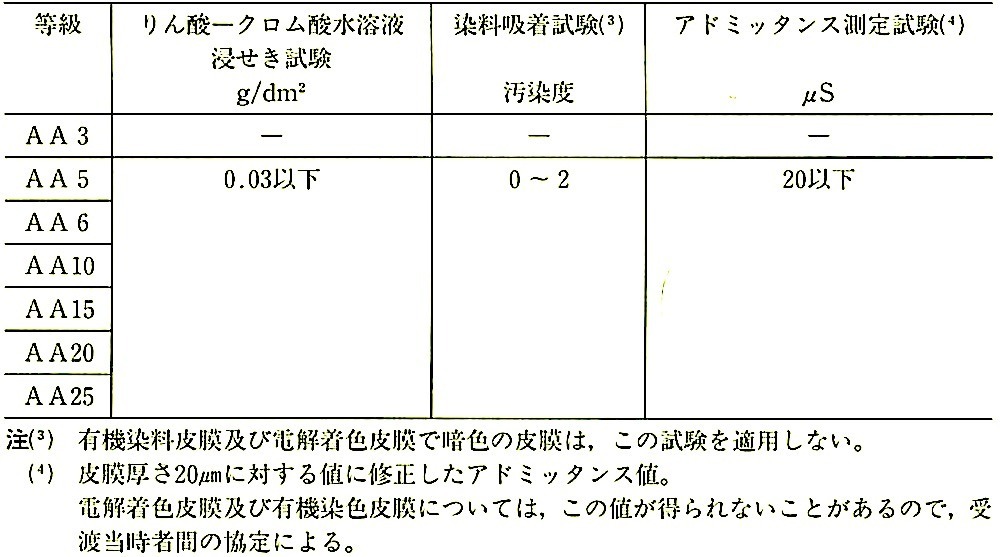
JIS H 8601 : 1999
(e) 陽極酸化塗装複合皮膜の性能
陽極酸化塗装複合皮膜の性能については、JIS H 8602(アルミニウム及びアルミニウム合金の陽極酸化塗装複合皮膜)に規定されており、その抜粋を次に示す。
また、適用環境(参考)における区分をJIS Z 2381(大気暴露試験方法通則)により示す。
なお、JIS規格中の各試験方法については(g)による。
4 種 類
複合皮膜の種類は、複合耐食性及び耐候性によって区分し、表1の4種類とする。なお、種類は、複合耐食性及び耐候性の両方の性能を満足しなければならない。
表1– 陽極酸化塗装複合皮膜の種類
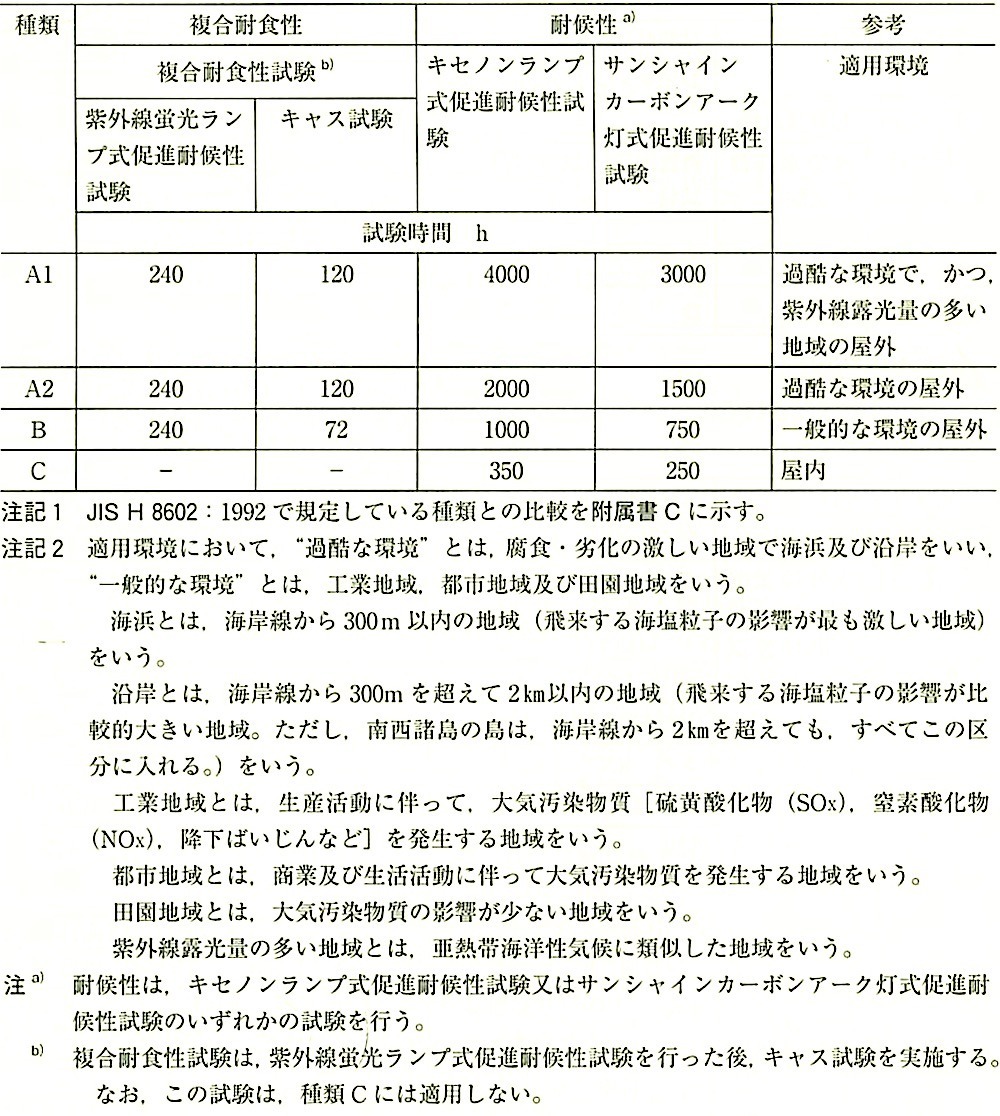
5 品 質
5.1 外 観
外観は6.3によって試験を行い、きず、むらはがれなどの使用する上で問題となる欠点があってはならない。
なお、使用する上で問題となる欠点の判断は、受渡当事者間の協定による。欠点の程度は、限度見本によって示すのが望ましい。
5.2 性 能
複合皮膜の性能は、箇条6によって試験を行い、表2による。
表2 陽極酸化塗装複合皮膜の性能
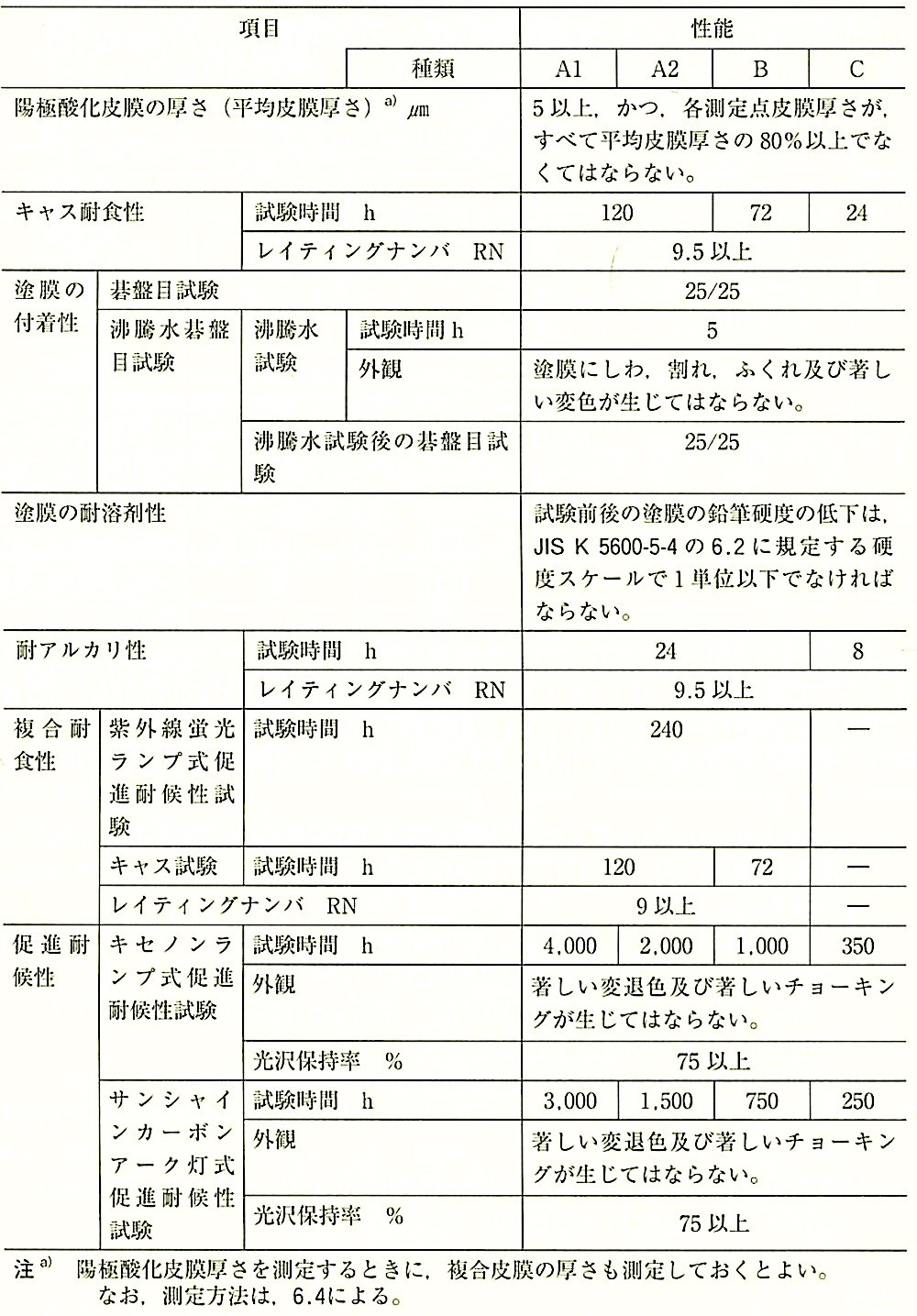
附属書 C (参考)種類
序 文
この附属書は、本体に規定する種類とJIS H 8602 : 1992に規定する種類との対比を示すもので、規定の一部ではない。
C.1 種 類
種類の対比を表C.1に示す。
表C.1 – 種類の対比

JIS H 8602 : 2010
附属書1(参考) 暴露環境の区分
1.2 日本の気候の区分
日本の気候区分は世界的に広く使われている植生の分布に基づいて作成されたケッペンの気候区分によると、北海道は、’’冷帯多雨気候型”、その他の日本各地は、沖縄まで含めて”温帯多雨気候型”に区分される (2) 。気温・降水量・日照率・水分過剰量の四つの気象要索による代表的な日本の気候区分”開口による日本の気候区分 (2) ”をベースにし、金属材料の腐食度に注目して区分すると、次の九つの気候区分に区分できる (3) 。その気候区分図を、附属書1 図1に示す。
注 (2) 関口「教養の気象学」朝倉書店.p158
注 (3) 「鉄鋼系社会資本材料の耐候性・耐食性試験評価方法に係わる調査研究」平成8年度報告書、p50 社団法人日本建材産業協会
a) 北海道・西 北海道の日本海側
b) 北海道・東 オホーツク海、太平洋側
c) 太平洋・北 伊豆半島以北(関東・東北地方)の太平洋側、甲信地方
d) 太平洋・南 東海・中部・近畿・四国・九州地方の太平洋側
e) 瀬戸内海 四国・中国・九州地方の瀬戸内海側
f) 日本海・北 能登半島以北(北陸・東北地方)の日本海側
g)日本海・南 福井・近畿・中国地方の日本海側
h) 九州・西 玄界灘に面した九州西祁
i) 南西諸烏 鹿児島県の南部の島から琉球列島に属する島(亜熱帯海洋性気候に類似した地域)
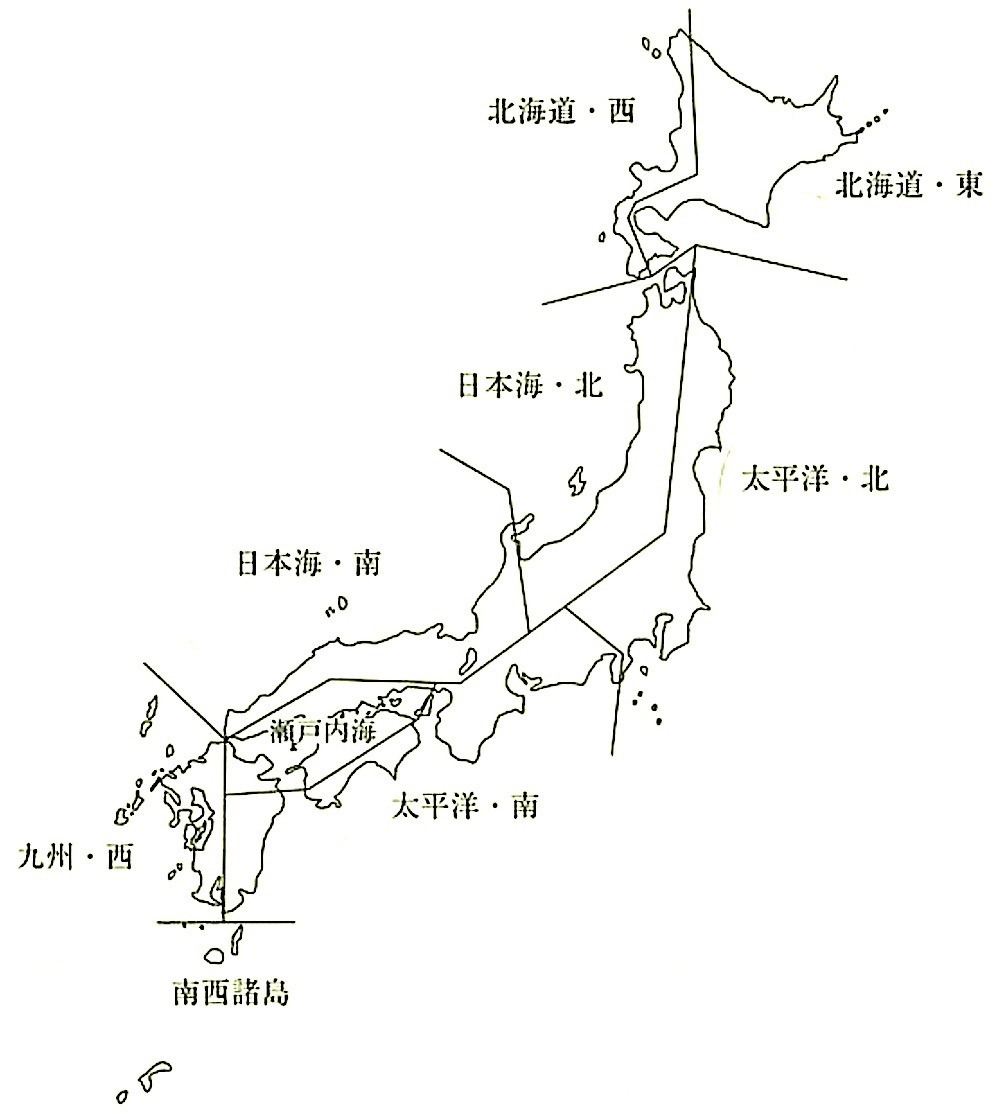
附属書1図1 日本の気象要素による気候区分
1.3 大気汚染区分(大気汚染物質による区分)
大気汚染物質[硫黄酸化物(SOx)、窒素酸化物(NOx)、降下ばいじんなど]の発生源及び飛来による影響、並びに火山、温泉などの特殊環境によって、次の五つの環境に区分する (3) 。
a) 工業地域 生産活動に伴って、大気汚染物質を発生する地域。
b) 都市地域 商業及び生活活動に伴って大気汚染物質を発生する地域。
c) 田園地域 大気汚染物質の影響が少ない地域。
d) 酸性雨地域 酸性雨の原因物質の直接の発生源ではないが、原因物質の飛来による影響の大きな地域。
e) 火山・温泉 火山性物質及び温泉からのガス(硫化水索ガスなど)の影響を大きく受ける地域(自然現象による特殊環境として区分する)。
1.4 海塩区分(海塩粒子の影響度合いによる区分)
金属材料の腐食に大きく関与する飛来海塩粒子の影響を考慮して、海岸線からの距離によって、次の五つの環境に区分する (3) 。
a) 海 上
b) 海 浜
海岸線から300m以内の地域(飛来する海塩粒子の影響が最も激しい地域)。
c) 沿 岸
海岸線から300mを超えて2km以内の地域(飛来する海塩粒子の影響が比較的大きい地域.ただし、南西諸島の島は、海岸線から2kmを超えても、すべてこの区分に入れる。)。
d) 準沿岸
海岸線から2kmを超えて20km以内の地域(飛来する海塩粒子の影響が比較的小さい地域)。
e) 内 陸
海岸線から20kmを超えた地域(飛来する海塩粒子の影響が無視できる地域)。
JIS Z 2381 : 2001
(f) 使用環境による表面処理の種類
JIS H 8601及び8602では表面処理の性能に応じた種類を規定しており、使用環境や用途に応じて適切に選定を行う必要がある。
使用環境に応じた表面処理の例を表14.2.3に示す。また、特殊な用途の表面処理の例を表14.2.6に示す。
表14.2.3 環境別表面処理基準
((-社)軽金属製品協会 ビル用アルミニウム建材の環境別表面処理基準より)
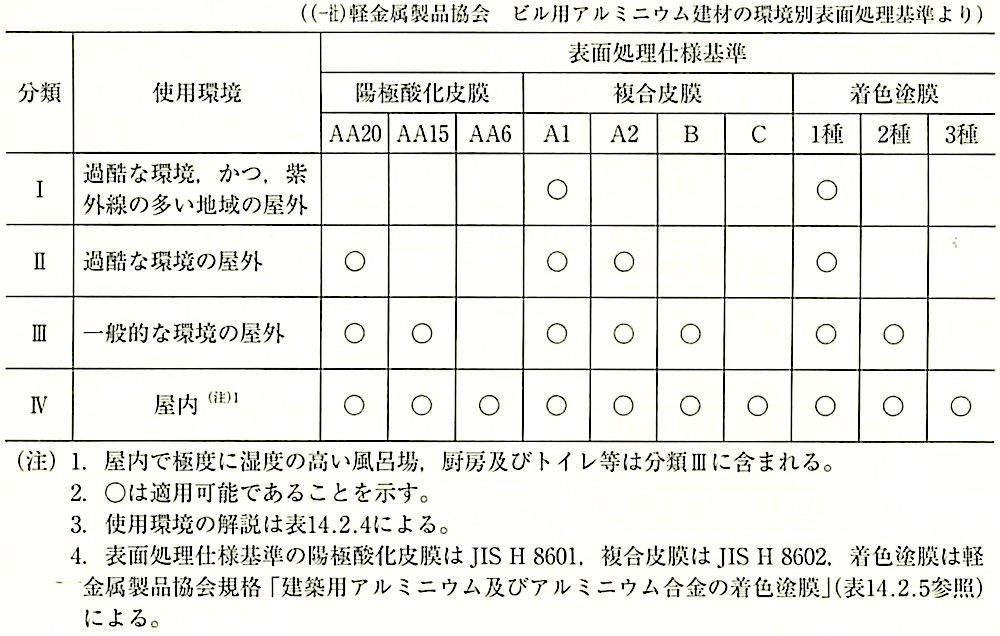
表14.2.4 使用環境の解説
((-社)軽金属製品協会 ビル用アルミニウム建材の閑税別表面処理基準より)
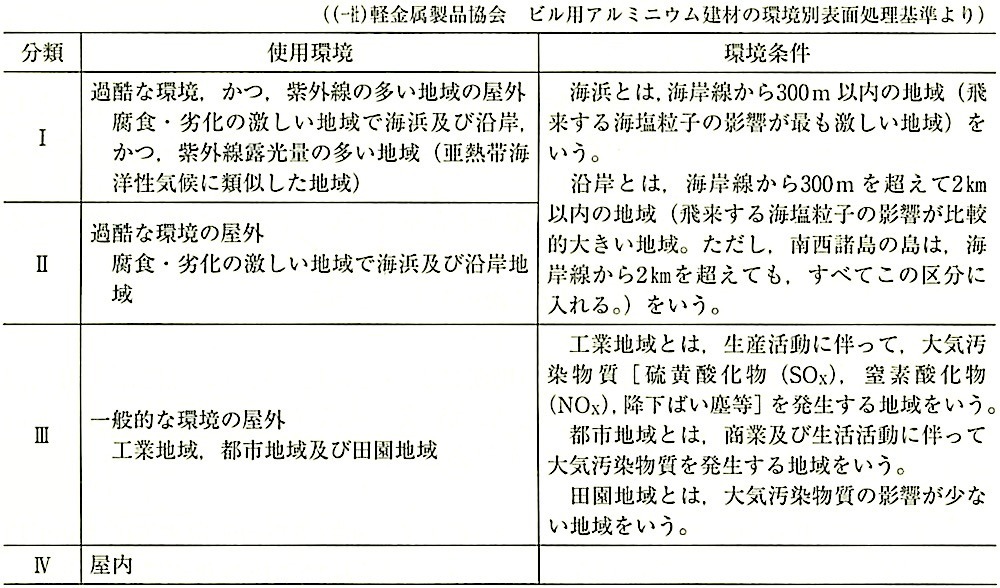
表14.2.5 種別による着色塗料の種類、厚さ及び塗装方法
((-社)軽金属製品協会規格 建築用アルミニウム及びアルミニウム合金の着色塗膜より)
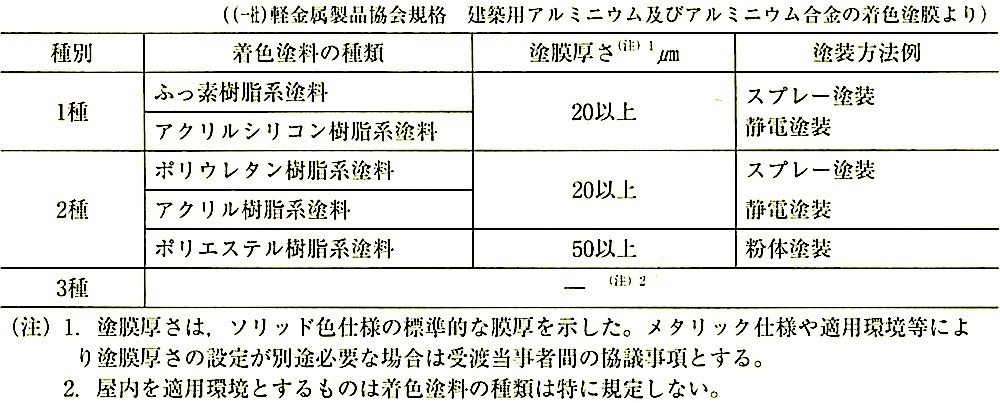
表14.2.6 特殊な用途の表面処理基準
((-社)軽金属製品協会 ビル用アルミニウム建材の環境別表面処理基準より)
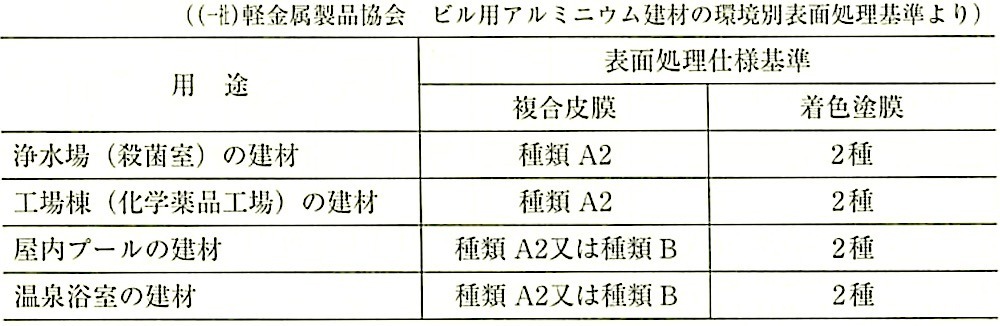
(g) 表面処理の試験
アルミニウムの表面処理の試験は、JIS H 8601.、 JIS H 8602.、JIS H 4001のそれぞれに規定されており、外観、皮膜、塗膜厚さ等のほか、用途に応じて当事者間の協議により行う項目もある。
設計図書で示された表面処理の性能及び品質を満足することを証明する資料としては製造所で通常生産されている製品であれば、その品質検査記録によることができる。
ただし、生産実績が少ない場合は、必要な試験を行い、品質及び性能を確認することとなる。
JISに規定する各試験項目の概要は、次のとおりである。
(i) 外観試験
外観試験は照度が600Ix以上の場所において目視で行う。光源は常用光源 D65、高演色形の蛍光ランプ(演色AAA)又は拡散昼光とする。背景は無光沢の黒、灰色等の無彩色であることが望ましい。
(ii) 陽極酸化皮膜厚さ試験
陽極酸化皮膜厚さ試験は渦電流式測定法又は顕微鏡断面測定法等により平均皮膜厚さ(μm)の測定を行う。複合皮膜の試験片は陽極酸化皮膜に損傷を与えない方法で塗膜を除去してもよい。
(iii) キャス試験
銅塩の添加で腐食作用を促進した酢酸酸性の塩水を噴霧し、皮膜や複合皮膜の耐食性を調べる試験。判定は発生した孔食をレイティングナンバにより評価する。
(iv) 塗膜の付着性試験
?@碁盤目試験
複合皮膜の塗膜に 1mm間隔(塗膜 0〜60μmの硬い素地に対して)で6本ずつのクロスカットを入れ、25のます目をつくる。セロハン粘着テープを塗膜に張り付け、その後引きはがす。このときにはがれた塗膜の状況により塗膜の付着性を評価する。塗膜のいずれのます目もはがれが認められないものを、25/25とする。
?A沸騰水碁盤目試験
複合皮膜の沸騰水試験は、脱イオン水を加熱した 95℃以上の沸騰水に試験片を5時間浸漬させ引き上げ、5min以内に塗膜の外観にしわ、割れ、ふくれ及び著しい変色等の有無を評価する。続いて、碁盤目試験により付着性を評価する。
(v) 塗膜の耐溶剤性試験
塗膜の耐溶剤性試験は、キシレンを浸した脱脂綿等で塗膜を30回往復して軽くこする。試験前後の塗膜の鉛筆硬さの変化によって耐溶剤性を評価する。
(vi) 耐アルカリ性
複合皮膜の耐アルカリ性試験は、5g/Lの水酸化ナトリウム水溶液を複合皮膜の表面に接触させて、発生した孔食及びふくれの発生程度をレイティングナンバで評価する。
(vii) 複合耐食性試験
複合皮膜の複合耐食性試験は、紫外線蛍光ランプ式促進耐候性試験を行ったのち、キャス試験を行い、外観及び腐食の発生程度をレイティングナンバで評価する。
(?G) 促進耐候性試験
複合皮膜の促進耐候性試験は、キセノンランプ式又はサンシャインカーボンアーク灯式促進耐候性試験機のいずれかにより所定時間の試験を行う。外観の変退色、チョーキングの程度及び光沢保持率により評価する。
(ix) 皮膜の封孔度試験
陽極酸化皮膜の封孔の効果を調べる試験。染料吸着試験及びりん酸ークロム酸水溶液浸漬試験等により評価を行う。
(x) 耐摩耗性試験
皮膜の耐摩耗性は噴射摩耗試験、砂落とし摩耗試験及び往復運動平面摩耗試験により評価する。噴射摩耗試験及び砂落とし摩耗試験は、皮膜に研磨材を噴射又は落下させ、皮膜が削り取られて素地が露出するまでの時間を測定する。往復運動平面摩耗試験は、装置の摩耗輪に研磨紙を張り付けた摩耗輪と試験片の間に一定の荷重を加えて往復連動させ、皮膜厚さの減少量を測定する。
14.2.3 鉄鋼の亜鉛めっき
(a) 亜鉛めっきの一般事項
(1) 「標仕」14.2.3には、鉄の防食を目的とする表面処理のうち、最も多く行われる亜鉛めっきについて定められている。
(2) 亜鉛の付着量は、「標仕」14.2.3(a)に定められているもののうちでは、溶融亜鉛めっきが多い。電気及び連続ラインによるものは、溶融亜鉛めっきよりはるかに少なく、大量に付着させるのは困難である。
(3) 亜鉛めっきの厚さと付着量は,14.2.1式の関係になる。
A=7.2 × t ・・・・・・(14.2.1 式)
A:亜鉛付着量(g/m 2 )
7.2:めっき皮膜の密度(g/cm 2 )
t :めっき膜厚(μm)
(4) 「標仕」の亜鉛めっき
(i) 「標仕」表14.2.2では亜鉛めっきの表面処理方法(溶融亜鉛めっき及び電気亜鉛めっき)やめっきの付着量により、A〜F種の種別が定められている。この他の亜鉛めっきとしては、従来の連続ラインにより製品化されていた表面処理亜鉛めっき鋼板類がある。
亜鉛めっきの種類とその使用箇所との関係は簡単には決められないが、目安を表14.2.7に示す。
表14.2.7 亜鉛めっきの種類と使用箇所
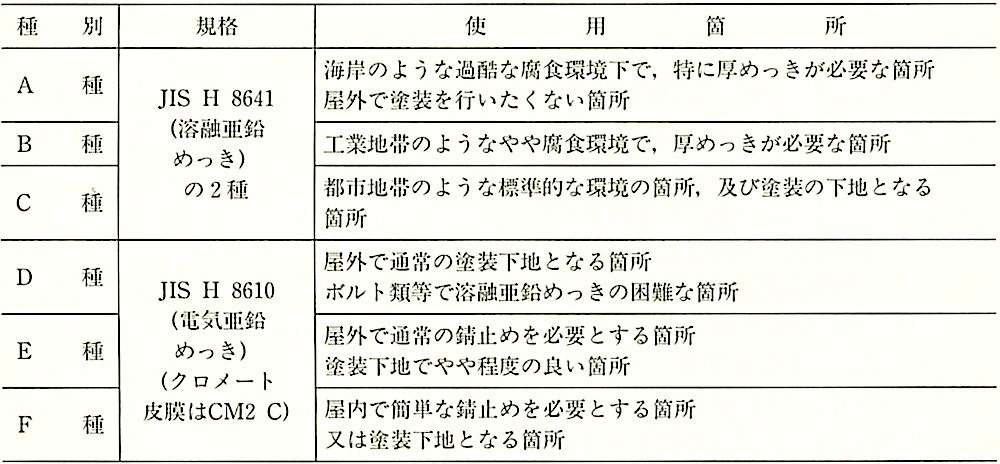
(ii) 「標仕」14.2.3(a)に定められている亜鉛めっきの通常の工程を図14.2.3及び4に示す。
?@ 溶融亜鉛めっきの工程
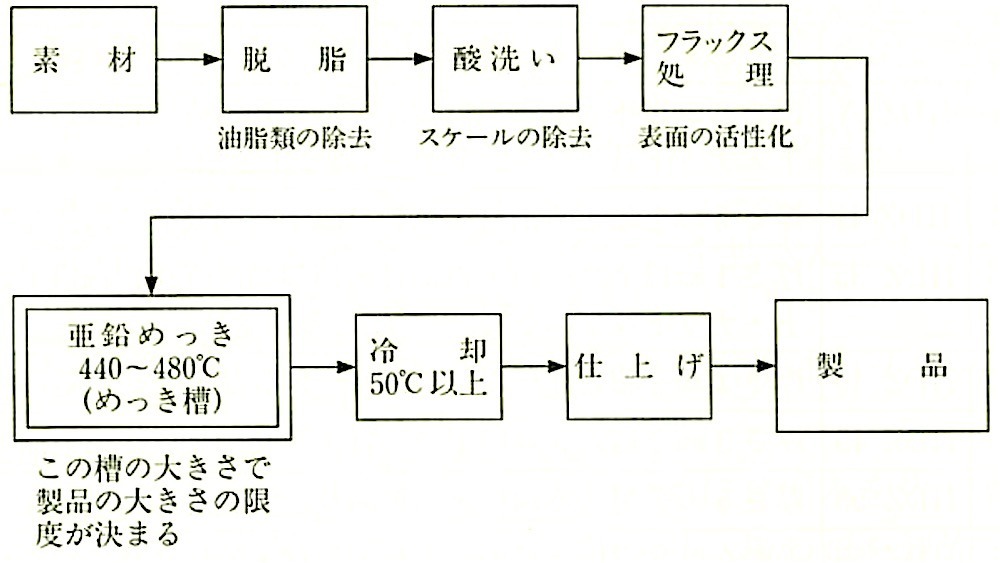
図14.2.3 溶融亜鉛めっきの工程
?A 電気亜鉛めっきの工程
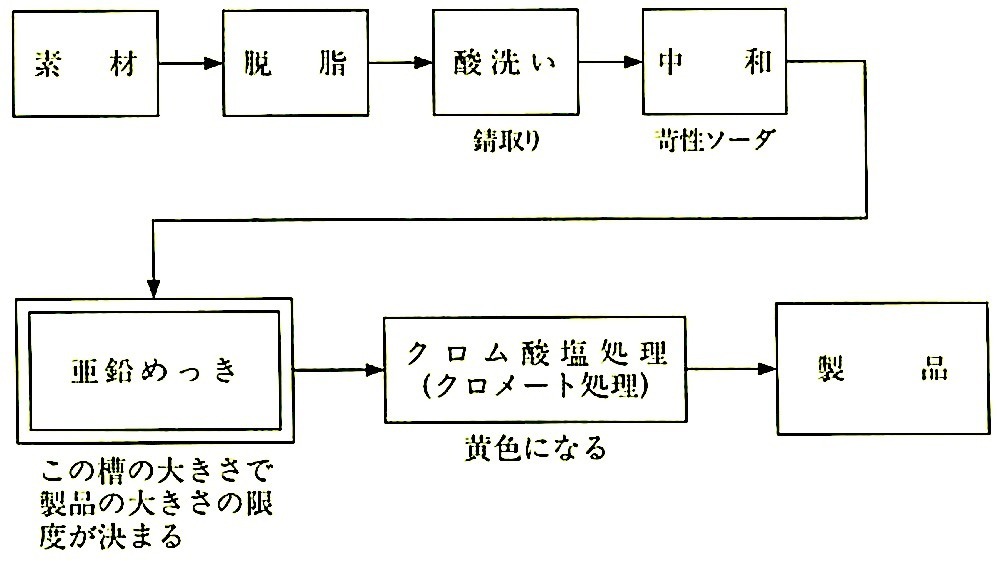
図14.2.4 電気亜鉛めっきの工程
(b) 亜鉛めっきの各論
(1) 溶融亜鉛めっき
(i) 溶融亜鉛めっきは、溶融した亜鉛の中に鉄材を浸せきして、亜鉛めっき皮膜を生成させる方法である(どぶづけめっきとも呼ばれている。)。
(ii) めっきは素地とよく密着し、使用に際してはく離を起こしてはならない。
(iii) JIS H 8641(溶融亜鉛めっき)による溶融亜鉛めっきの種類等を次に示す。
4. 種類及び記号
めっきの種類及び記号は、表1による。
表1 種類及び記号
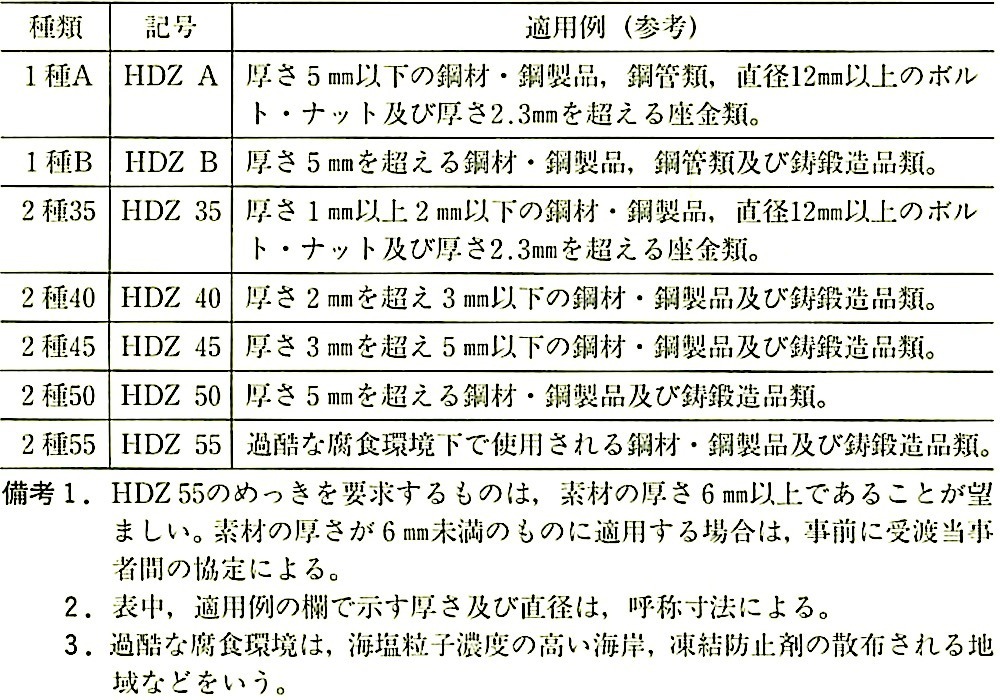
6. めっきの品質
めっきの品質は、次による。
6.2 付着量及び硫酸銅試験回数
めっきの付着量は、7.3の試験を行ったとき、表2に適合しなければならない。硫酸銅試験同数は、表2の試験回数とし、7.4の試験を行ったとき、JIS H 0401の 6.8に規定する判定基準を満足しなければならない(7.3. 7.4省略)。
表2 付着量及び硫酸銅試験回数
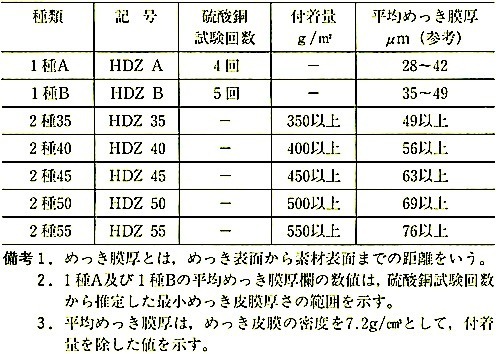
(iv) 施工上の主な留意事項
?@ めっき工場に設備された製品を浸せきする槽の大きさ等により、一度にめっきできる部品の大きさが制限されるので、施工図を検討する際には細手位置等の検討を行い、最大部品の大きさとめっき槽との関係を検討しておく。特に規模の大きい工場がない地方では注意が必要である((a)(4)(ii)参照)。
?A 密封した部分や空洞があると、ピンホール等から水分が浸入し,めっき槽に浸せきした際、急激に膨張し爆発することがあるので、このような部分をつくってはならない。
?B 可動部分で擦れ合う箇所は、めっき厚さを見込んだ十分な余裕がないとめっきにより動きが悪くなる。
ボルト、ナットの場合は、ナットのねじを普通より大きめにしておくか、めっき後ねじ部の亜鉛をさらう必要がある。
?C 板厚の薄い製品をめっきすると、熱のためにひずみを生じやすいため、板厚により亜鉛の付着量に限度がある。手すり、柵の類を製作するときに起こりやすいので注意する。
?D 溶接部には、アンダーカット、ピット、割れ等があってはならない。また、スラグは入念に除去されていなければならない。
(v) 溶融亜鉛めっきのめっき厚さは、部材を構成する板厚が異っている場合、薄い部材で決まってしまうため、「標仕」表14.2.2では最小板厚の規定をしている。
(2) 電気亜鉛めっき
(?@) JIS H 8610(電気亜鉛めっき)に定められている電気亜鉛めっきの等級は表14.2.8のとおりである。
表14.2.8めっきの等級及びめっきの最小厚さ
(JIS H 8610 : 1999)
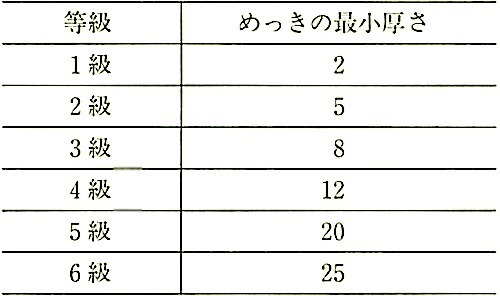
(ii) 「標仕」表14.2.2では、クロメート皮膜は JIS H 8625(電気亜鉛めっき及び電気カドミウムめっき上のクロメート皮膜)によるCM2 Cが指定されている。
(iii) 電気亜鉛めっきは、めっきの層が薄く短時間に防錆効果が失われるので、そのままで使用されることは少ない。
特に屋外においては、めっきの上に塗装するのが原則である。塗装については、18章を参照する。
(3) 表面処理亜鉛めっき鋼板
表14.2.7に示すように、表面処理亜鉛めっき鋼板には溶融亜鉛めっきによる方法及び電気亜鉛めっきによる方法とがあり、ともに工場生産品である。
?@ 溶融亜鉛めっき鋼板及び鋼帯のめっきの最小付着量については,JIS G 3302(溶融亜鉛めっき鋼板及び鋼帯)に規定されている。
?A 電気亜鉛めっき鋼板及び鋼帯については JIS G 3313(電気亜鉛めっき鋼板及び鋼帯)に規定されている。そのめっきの付着量の抜粋を次に示す。
4. 1 めっきの付着量
めっきの付着量は、12.1.2によって試験を行い、それぞれの試験片の片面ごとの最小付着量は表4による。ただし、附属書 JEによってめっきの付着量を測定する場合には、JE.6.5によって求めた測定値のそれぞれに適用する。
板及びコイルには、両面のめっきの付着量が同一のもの(以下、等厚めっきという。)、両面のめっきの付着量が異なるもの(以下、差厚めっきという。)及び片面だけめっきしたもの(以下、片面めっきという。)がある。
4.2 めっきの付着量表示記号
めっきの付着量表示記号は、表4のめっきの片面付着量表示記号の組合せととしその表し方は次による。
a) 板の場合は、めっきの片面付着量表示記号を、積載された板の上面/下面の順に表す。
例1 E16/E16
b) コイルの場合は、めっきの片面付着量表示記号を、コイルの外面/内面の順に表す。
例2 E16/E32
c) 片面めっきの場合は、鉄面の片面付着量表示記号(ES)/板又はコイルの面のめっきの片面付着量表示記号の順に表す。
例3 ES/E40
d) 必要に応じて板又はコイルに差厚めっきであることを表すマークを付ける場合は、マークを付けた面のめっきの片面付着量表示記号の後にDを付記する。
例4 E8/E16D
表4 – めっきの付着量表示記号及び片面の最小付着量
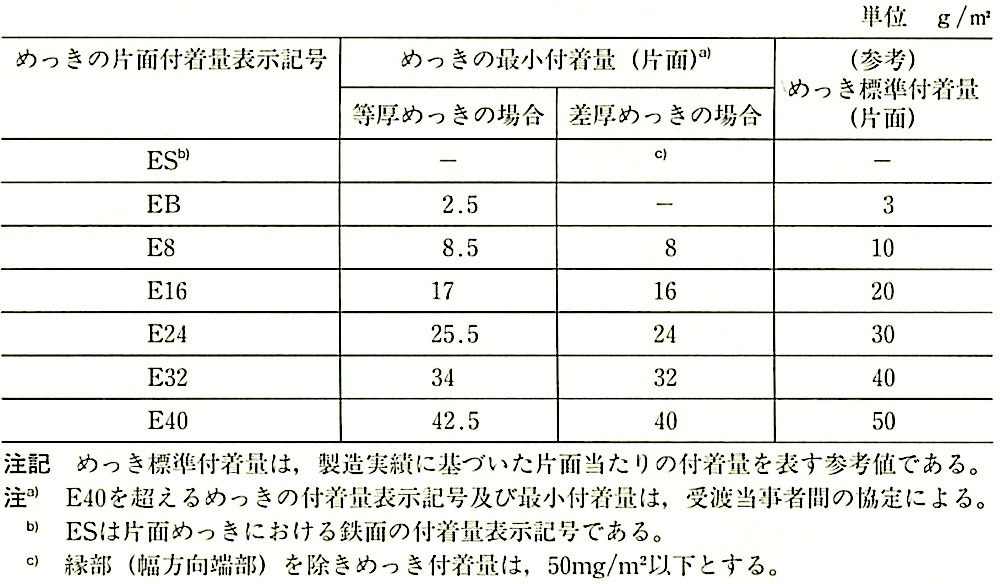
JIS G 3313: 2010
(c) 鉄鋼の亜鉛めっきの検査
(1) 亜鉛めっきの膜厚測定
亜鉛めっきの付着量は、膜厚を測定すれば、14.2.3(a)(3)の 14.2.1式により求めることができる。膜厚測定器としては、非破壊で簡便な電磁厚み計がある。これは、多少誤差が大きいが、概略の付着量を知るのに適しているので、現場における施工管理の参考として利用できる。
測定は、1箇所につき5回以上とし、平均値をその箇所の厚さとする。
なお、亜鉛めっきの膜厚測定は、JISでは電気亜鉛めっきについてのみ規定している((2)(ii)参照)。
(2) 亜鉛めっきの試験
(i) JISによる亜鉛めっきの試験は、付着量試験として直接法と関接法、硫酸銅試験、密着性試験、性状試験等がある。
?@ 付着量試験では、一般に塩化アンチモン液又はヘキサメチレンテトラミン液を用いる間接法で行われるが、これは破壊試験となるので、製品と同等な条件で作られた試験片(10cm角程度)で行うことになる。
?A 直接法は、素材の表面積及び質量の測定が可能なものに限られるため、小さい金物類に適用される。
?B硫酸銅試験は、最小膜厚を調べるもので、塩化アンチモン液又はヘキサメチレンテトラミン液を用いる関接法と同様な試験片を用いて行う。
?C 密着性試験と性状試験は、通常行われていない。
JISによる試験の適用を表14.2.9に示す。
表14.2.9 試験方法の適用(JIS H 0401 : 2013)

(ii) 電気亜鉛めっきの皮膜厚さ試験は、JIS H 8610に次の方法が規定されている。
?@ 顕微鏡断面試験方法
?A 磁力式試験方法
?B 電解式試験方法
?C 蛍光X線式試験方法
?D β線式試験方法
?E 測微計による試験方法の中の触針走査法
?F 質量計測によるめっき付着量試験方法の中のめっき破壊質量法
(iii) 表面処理亜鉛めっき鋼板における溶融亜鉛めっき鋼板のめっきの付着量試験は、JIS G 3302のめっきの付着量試験による。また、電気亜鉛めっき鋼板のめっきの付着量試験は、JIS G 3313のめっきの付着量試験による。
(d) 溶融亜鉛めっき面の仕上り及び補修について
(1) 溶融亜鉛めっき面の仕上り外観
溶融亜鉛めっき面の仕上り外観については、JIS H 8641(溶融亜鉛めっき)による。次にその抜粋を示す。
3.2 めっき表面に見られる諸現象
a) 不めっき
局部的にめっき皮膜がなく,素材面の面出しているもの。
参考
不めっきが小さい場合は、周辺亜鉛の犠牲的保護作用によって耐食上あまり影響はない。保護作用の効果が及ぶ不めっき部の大きさは、実験的には、φ5.5mm又は5mm幅までである。
b) や け
金属亜鉛の光沢がなく、表面がつや消し又は灰色を呈したもの。甚だしい場合には暗灰色となる。
参考
この現象は合金層がめっき表面に露出したものであり、大気中での耐食性には影響ない。やけは、密着性さえ十分であれば実用上の欠陥とはならないので、外観基準を設定する場合は、この点を考慮することが必要である。
なお、金属亜鉛の光沢は酸化の進行とともに失われ、やけの表面と類似した色調となってくる。素材の鋼製造工程(脱酸法)によってけい素含有量に違いがあり、その影響でやけの発生頻度に差が生じる。
c) た れ
端部又は部分的に、亜鉛が多量に付着しているもの。
参考
一般的にやけの発生しやすい素材は、めっき温度を低くしてめっき作業をするため亜鉛の流動性が低下し、たれを発生させてしまうことが多い。たれの部分をやすりなどで研磨し、平滑面を得ようとするときは、素材表面を露出させないようにする。実用上障害とならない限りそのままにしておいたほうがよい。
d) シーム
素材にきずがあると、めっきしたときに、めっき表面に特徴ある線状の凹凸になるめっき。
参考
シームは、通常めっき皮膜が形成されているので、そのまま使用しても問題はない。しかし、その面を平滑にしようとすると素材表面を露出することがある。
e) かすびき
表面に亜鉛酸化物又はフラックス残さが著しく付着しているもの。
参考
一般に耐食性に影響がある。したがって、付着した場合はやすりなどで除去しておくほうがよい。
f) ざらつき
微粒状の突起があり、懸濁(けんだく)浮遊物質(ドロス)が付着した部分。
参考
耐食性には影響はない。
g) き ず
めっき作業中、めっき用具とめっき表面とが接触したこん(痕)。
参考
めっき表面のきずは、発生位置、大きさ及び深さによってその有害性を判断する必要がある。
h) 変 色
保管中の薬品などの付着及びめっき浴からの引上げ時に、めっき表面が変色したもの。
参考
めっき引上げ時に生じる変色は、光の干渉・反射に起因したもので、耐食性に影響はない。
i) 白さび
保管中に雨水の付着、結露などによって生じた塩基性炭酸亜鉛などの腐食生成物。
参考
白さびによるめっき皮膜の消耗はわずかで、耐食性にはほとんど影響はない。
6. めっきの品質
めっきの品質は、次による。
6.1 外 観
めっきの外観は、受渡当事者間の協定による用途に対して使用上支障のある不めっきなどがあってはならない。また、めっき表面に現れる耐食性にはほとんど影響のない、濃淡のくすみ(やけなど)及び湿気によるしみ(白さびなど)によって合否を判定してはならない。
備考
めっきの主目的は、耐食性にあり、美観的要求事項を渦足させることではない。
また、装飾の目的で施されるものでもない。めっきは表面素材を滑らかにすると考えがちであるが、素材表面より良くならないのが普通である。
JIS H 8641 : 2007
(2) めっき面の欠陥部分の補修
溶融亜鉛めっき面について不めっき、傷、かすびき、摩擦面のたれ等があるものに関しては、「標仕」表14.2.4により補修を行う。