01節 共通事項
18.1.1 一般事項
(1) この章は、美装及び防食を目的とした建築物の内外部の塗装工事を対象としている。
対象とする素地は、木部、鉄鋼面・亜鉛めっき鋼面及びモルタル面・プラスター面等の左官塗り面、コンクリート面・ALCパネル面・押出成形セメント板面、せっこうボード・その他のボード面等である。
「標仕」での塗装工事は、一般的な工事現場(一部工場等)で行う常温での塗装を想定しており、工場等で行う焼付け塗装については対象外である。
なお、「標仕」各節名称( )内の略号は、原則的には「JASS 18 塗装工事」に準拠したものである。
(2) 作業の流れを図18.1.1に示す。
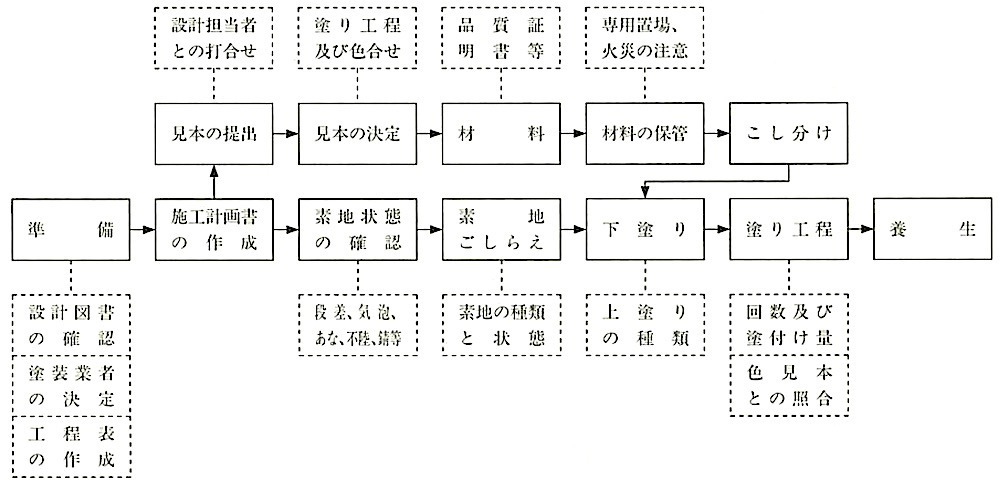
図18.1.1 塗装工事の作業の流れ
(3) 施工計画書の記載事項は、概ね次のとおりである。
なお、を考慮しながら品質計画を検討する。
?@ 工程表(色見本の決定、施工(全体、部屋別、階別等)等の時期)
?A 製造所名、施工業者名及び作業の管理組織
?B 塗装箇所及び素地若しくは下地の材料の種類による塗料の種別(防火材料の指定がある場合には認定品)並びに工程
?C 色調別による塗装範囲
?D 工場及び現場塗装の区分
?E 工法(はけ、吹付け、ローラー等)
?F 養生方法(施工中及び完了後)
?G 塗料の保管方法、安全管理の方法等
18.1.2 基本要求品質
(1) 塗装は建築物の内外部に施され、仕上げとしての美装の目的のみでなく、各種劣化外力(雨水、結露水、飛散・浮遊物質、二酸化炭素ガス、紫外線等)から塗装された材料を保護することによって、建築物の耐久性を向上させることを目的としている。
塗膜の性能に影響を及ぼす要因の一つとして、使用する塗料の耐久性があげられる。これは上塗り塗料だけでなく、中塗り、下塗り及び素地ごしらえに用いる材料についても同様である。これらの材料によって総合的な塗膜が構成され、硬化塗膜としての性能を発揮する。
したがって、塗装に使用する塗料その他の材料は、定められた品質及び性能を有するものとし、そのことが分かるように整理しておかなければならない。
(2) 塗装仕上り面の出来ばえとしての要求は、各塗り工程の種別であるA種、B種等としてグレードを指定される。実際の工事に際しては、要求に合わせて塗装部位ごとに、どの程度の出来ばえとするかをあらかじめ品質計画で定めておくことが必要である。
この仕上り面は、最終の上塗りだけではなく、各塗り工程ごとで考えるようにする。例えば、下塗りであれば次に塗る中塗りとの付着性を確保できるような面の状態となるように仕上げるとともに、所定の表面状態とする。
塗料の種類と塗装工程の組合せによっても、塗装の仕上りが異なることに注意することが重要である。
「標仕」では、一般的な塗装工程を考慮して、指定する標準的な工法、塗付け量、工程間隔時間及び最終養生時間等を守れば、所要の表面状態を確保できるようになっている。
(3) 硬化塗膜に対する要求性能としては、使用する塗料だけではなく適正な塗装工程との組合せで示されている。
塗膜は、所定の材料を所定の塗付け量、塗り工程で施工することによって要求される耐久性を有し、素地の耐火性等の性能を損なうものであってはならない。そのためには、これらの性能を阻害するような欠陥がない塗膜にすることは当然である。
塗膜の構成は耐久性に及ぼす影響が大きく、例えば、素地や塗膜の表面を調整するために使用するパテ材料の介在が著しい場合には耐久性が劣ってくる。このようなことを避けるためには、塗り工程の前に施す素地ごしらえの段階で、適切な処理を十分に行うことが重要である。
塗料に対する防火材料の認定は、所定の塗膜厚さで基材と同等の防火性能をもっものとして認められているものである。出来ばえを重視して、いたずらに厚く塗り過ぎることは防火性能に悪影響を及ぽすため、避けなければならない。
18.1.3 材料
(1)「標仕」では、屋内で使用する材料の選定に当たっては、揮発性有機化合物の放散による健康への影響に配慮することにしている。
本章では、シックハウス症候群の原因物質の一つであると考えられているホルムアルデヒドに関して、屋内で使用する塗料からの放散量は、JIS等の材料規格において放散等級の規定がある場合には特記によることとし、特記がなければ、F☆☆☆☆の塗料を用いることにしている。
建築基準法に関連するシックハウス症候群対策及びホルムアルデヒド放散量等の詳細、また、告示対象及び告示対象外でJIS等に放散等級等が規定されている塗料の表示とその確認方法等は、19章10節を参照されたい。
(2)「標仕」では、防火材料の指定がある場合は、建築基準法に基づき、指定又は認定を受けたものとしている。防火材科の確認は、(-社)日本塗料工業会の防火材料等証明書又は製品容器の表示マークによればよい。図18.1.2に表示マークの例を示す。
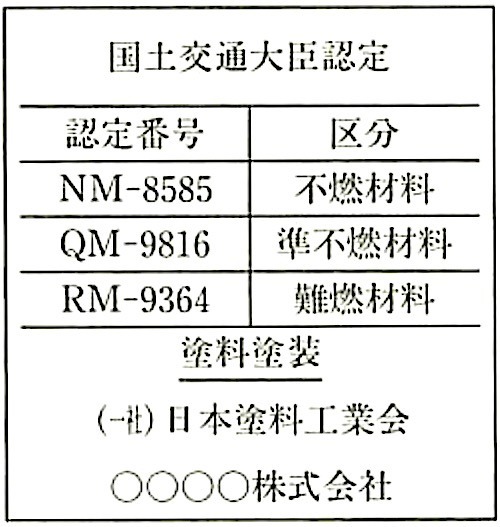
図18.1.2 製品容器の表示マークの例
(3) 塗料の色は、繊細なものであり、大量の塗料を現場において混合して同じ色調とすることは不可能に近い。このため、上塗塗料は指定した色の色彩や品質にばらつきが生じないよう、製造所において調合を行う。
製造所での調合には、所定の期間が必要であるため、工程に適合する時期に設計担当者と色彩計画を打ち合わせて決定する。
なお、一度に調色することが可能な少量の場合に限って、標仕では、同一の上塗登料の製造所の塗料を用いて現場調色することを認めている。
(4) 「標仕」では、塗装に用いる副資材は上塗塗料の製造所が指定する製品とすることを規定している。
(5) 「標仕」で規定された塗付け量は被塗物に塗り付けた量を示し、ロスを含まない。塗付け量を測定する場合は平らな面で行う。また、施工時に調整用として加えたシンナー等は含まないものとする。
(6) 塗料の種類と適用素地
(ア)「標仕」で規定している塗料の種類と適用素地との組合せを、表18.1.1に示す。
(イ)「標仕」では規定していないその他の主な塗料の種類と特徴を、表18.1.2に示す。
表18.1.1 塗料の種類と適用素地
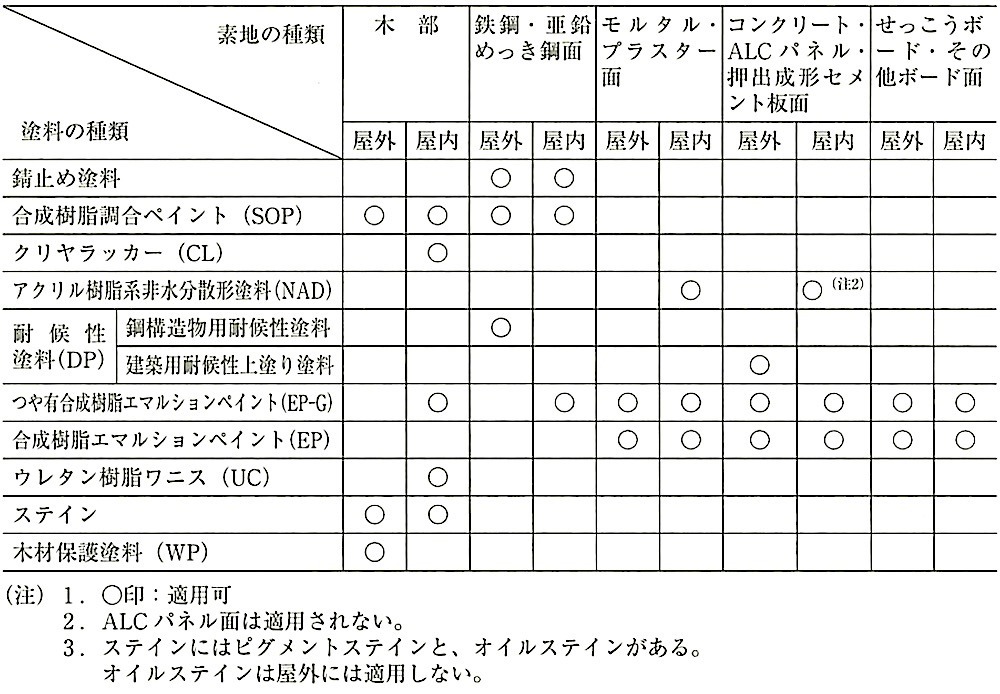
表18.1.2 「標仕」に規定されていない主な塗料の種類と特徴
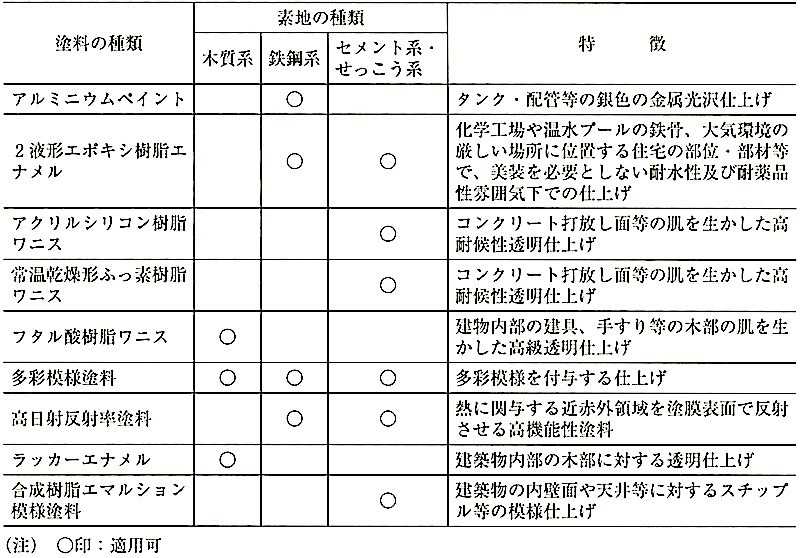
18.1.4 施工一般
(1) 塗装準備
(ア) 塗料の状態
(a) 搬入された塗料及び溶剤(シンナー)は、消防法等による危険物に指定されているものが多く、保管、貯蔵に当たっては、これら法令等を厳守しなければならない。
(b) 消防法関連法令とその略称を表18.1.3に示す。
表18.1.3 消防法関連法令とその略称
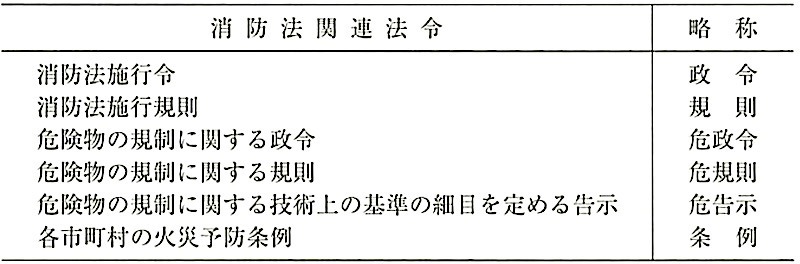
(c) 危険物と指定された塗料容器には、危険物の類別、危険物の等級について図18.1.3の例に示すような表示をすることが義務付けられており、この内容に応じた対応をしなければならない。
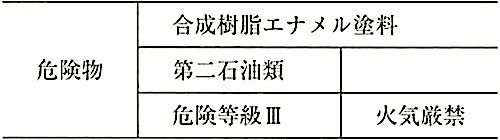
図18.1.3 危険物の種別、等級の表示の例
なお、消防法で定められる第四類(引火性液体)となる危険物の等級区分は、次のとおりである。
?@ 危険等級 ?T :特殊引火物(発火点が100℃以下のもの又は引火点が−20℃以下で沸点が40℃以下のもの)
?A 危険等級?U:第一石油類(引火点21℃未満のもの)とアルコール類(炭素の原子数が1〜3個までの飽和一価アルコール)
?B 危険等級?V:第二石油類(引火点が21℃以上70℃未満のもの)、第三石油類(引火点が70℃以上200℃未満のもの)、第四石油類(引火点が200℃以上250℃未満のもの)、動植物油類(引火点が 250℃未満のもの)
(d) 現場で使用する塗料関係の危険物の指定、貯蔵等についての消防法及び関連法令の関連部分の抜粋を次に示す。
〇 消防法(昭和23年法律第186号、最終改正令和3年5月19日法律第36号)
第2条
この法律の用語は左の例による。
?F 危険物とは、別表第1の品名欄に掲げる物品で、同表に定める区分に応じ同表の性質欄に掲げる性状を有するものをいう。
(危険物等の貯蔵等の基準設定の市町村条例への委任)
第9条の4
危険物についてその危険性を勘案して政令で定める数量(以下「指定数量」という。)未満の危険物及びわら製品、木毛その他の物品で火災が発生した場合にその拡大が速やかであり、又は消火の活動が著しく困難となるものとして政令で定めるもの(以下「指定可燃物」という。)その他指定可燃物に類する物品の貯蔵及び取扱いの技術上の基準は、市町村条例でこれを定める。
?A 指定数量未満の危険物及び指定可燃物その他指定可燃物に類する物品を貯蔵し、又は取り扱う場所の位置、構造及び設備の技術上の基準(第十七条第一項の消防用設備等の技術上の基準を除く。)は、市町村条例で定める。
(危険物の貯蔵及び取扱いの制限等)
第10条
指定数量以上の危険物は、貯蔵所(車両に固定されたタンクにおいて危険物を貯蔵し、又は取り扱う貯蔵所(以下「移動タンク貯蔵所」という。)を含む。以下同じ。)以外の場所でこれを貯蔵し、又は製造所、貯蔵所及び取扱所以外の場所でこれを取り扱ってはならない。ただし、所轄消防長又は消防署長の承認を受けて指定数量以上の危険物を、10日以内の期間、仮に貯蔵し、又は取り扱う場合は、この限りでない。
?A 別表第1に掲げる品名(第11条の4第1項において単に「品名」という。)又は指定数量を異にする2以上の危険物を同一の場所で貯蔵し、又は取り扱う場合において、当該貯蔵又は取扱いに係るそれぞれの危険物の数量を当該危険物の指定数量で除し、その商の和が1以上となるときは、当該場所は、指定数量以上の危険物を貯蔵し、又は取り扱つているものとみなす。
?B 製造所、貯蔵所又は取扱所においてする危険物の貯蔵又は取扱いは、政令で定める技術上の基準に従つてこれをしなければならない。
?C 製造所、貯蔵所及び取扱所の位置、構造及び設備の技術上の基準は、政令でこれを定める。
(危険物取扱者)
第13条
政令で定める製造所、貯蔵所又は取扱所の所有者、管理者又は占有者は、甲種危険物取扱者(甲種危険物取扱者免状の交付を受けている者をいう。以下同じ。)又は乙種危険物取扱者(乙種危険物取扱者免状の交付を受けている者をいう。以下同じ。)で、 6月以上危険物取扱いの実務経験を有するもののうちから危険物保安監督者を定め、総務省令で定めるところにより、その者が取り扱うことができる危険物の取扱作業に関して保安の監督をさせなければならない。
?A 製造所、貯蔵所又は取扱所の所有者、管理者又は占有者は、前項の規定により危険物保安監督者を定めたときは、遅滞なくその旨を市町村長等に届け出なければならない。これを解任したときも、同様とする。
?B 製造所、貯蔵所及び取扱所においては、危険物取扱者(危険物取扱者免状の交付を受けている者をいう。以下同じ。)以外の者は、甲種危険物取扱者又は乙種危険物取扱者が立ち会わなければ、危険物を取り扱ってはならない。
別表第1 (第2条、第10条、第11条の4関係)第四類抜粋
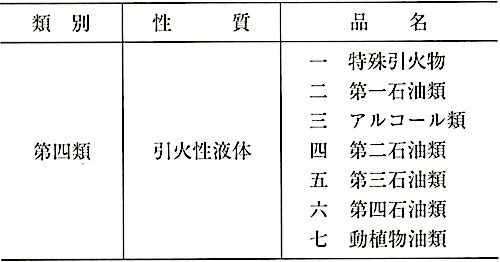
備 考
十
引火性液体とは、液体(第三石油類、第四石油類及び動植物油類にあっては、1気圧において、温度20度で液状であるものに限る。)であって、引火の危険性を判断するための政令で定める試験において引火性を示すものであることをいう。
十一
特殊引火物とは、ジエチルエーテル、二硫化炭素その他1気圧において、発火点が100度以下のもの又は引火点が零下20度以下で沸点が40度以下のものをいう。
十二
第一石油類とは、アセトン、ガソリンその他1気圧において引火点が21度未満のものをいう。
十三
アルコール類とは、1分子を構成する炭素の原子の数が1個から3個までの飽和一価アルコール(変性アルコールを含む。)をいい、組成等を勘案して総務省令で定めるものを除く。
十四
第二石油類とは、灯油、軽油その他1気圧において引火点が21度以上70度未満のものをいい、塗料類その他の物品であって、組成等を勘案して総務省令で定めるものを除く。
十五
第三石油類とは、重油、クレオソート油その他1気圧において引火点が70度以上200度未満のものをいい、塗料類その他の物品であって、組成を勘案して総務省令で定めるものを除く。
十六
第四石油類とは、ギヤー油、シリンダー油その他1気圧において引火点が200度以上250度未満のものをいい、塗料類その他の物品であって、組成を勘案して総務省令で定めるものを除く。
十七
動植物油類とは、動物の脂肉等又は植物の種子若しくは果肉から抽出したものであつて、1気圧において引火点が250度未満のものをいい、総務省令で定めるところにより貯蔵保管されているものを除く。
〇 危険物の規制に関する政令(昭利34年政令第306号、最終改正令和元年12月13日 政令第183号)
(危険物の指定数量)
第1条の11
法第9条の4の政令で定める数量(以下「指定数量」という。)は、別表第三の類別欄に掲げる類、同表の品名欄に掲げる品名及び同表の性質欄に掲げる性状に応じ、それぞれ同表の指定数量欄に定める数量とする。
(指定可燃物)
第1条の12
法第9条の4の物品で政令で定めるものは、別表第4の品名欄に掲げる物品で、同表の数量欄に定める数量以上のものとする。
(貯蔵所の区分)
第2条 法第10条の貯蔵所は、次のとおり区分する。
1 屋内の場所において危険物を貯蔵し、又は取り扱う貯蔵所(以下「屋内貯蔵所」という。)
(屋内貯蔵所の量準)
第10条 屋内貯蔵所(次項及び妨3項に定めるものを除く。)の位置、構造及び設備の技術上の基準は、次のとおりとする。(省略)
別表第3 (第1条の11 関係)第四類 抜粋
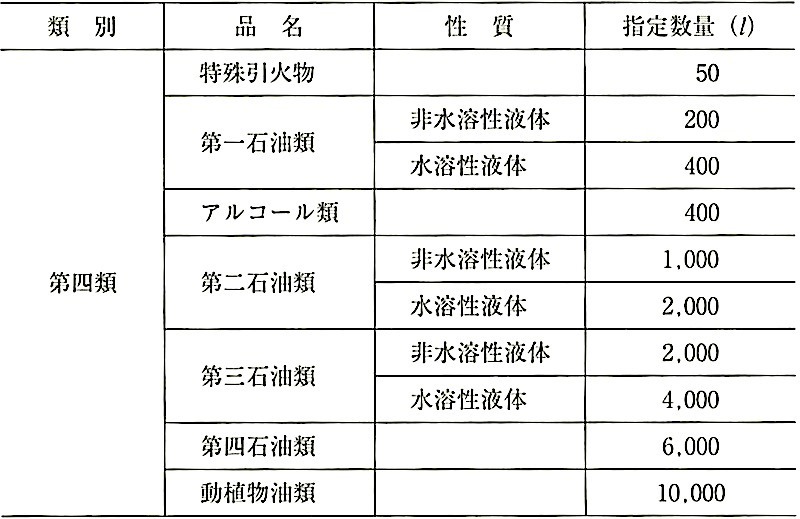
別表第4 (第1条の12関係)
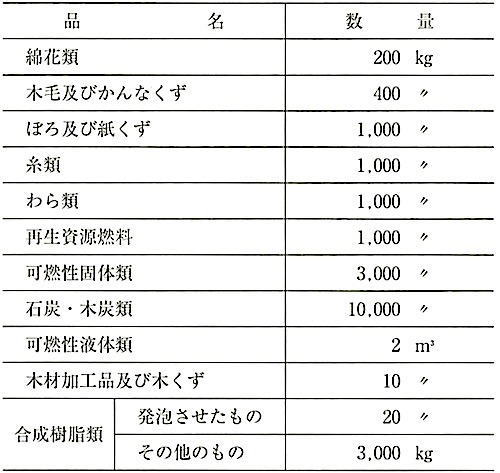
備 考
八
可燃性液体類とは、法別表第1備考第十四号の総務省令で定める物品で液体であるもの、同表備考第十五号及び第十六号の総務省令で定める物品で1気圧において温度20度で液状であるもの、同表備考第十七号の総務省令で定めるところにより貯蔵保
管されている動植物油で1気圧において温度20度で液状であるもの並びに引火性液体の性状を有する物品(1気圧において、温度20度で液状であるものに限る。)で1気圧において引火点が250度以上のものをいう。
〇 危険物の規制に関する規則(昭和34年総理府令第55号、最終改正令和3年7月21日総務省令第71号)
(品名から除外されるもの)
第1条の3
5 法別表第1 備考第十四号の組成等を勘案して総務省令で定めるものは、可燃性液体品が40パーセント以下であって、引火点が40度以上のもの(燃焼点が60度未満のものを除く。)とする。
6 法別表第1 備考第十五号及び十六号の組成を勘案して総務省令で定めるものは、可燃性液体量が40パーセント以下のものとする。
(e) 危険物貯蔵所の構造等に関して関係法令等には、主として次のような事項が定められている。
?@ 不燃材料で造った独立した平屋建てとし、周囲の建物から規定どおり離す。
?A 屋根は軽量な不燃材料で葺き、天井は設けない。
?B 建物内の置場は、耐火構造の室を選ぶ。
?C 床には不浸透性の材料を敷く。
?D 消火に有効な消火器、消火砂等を備える。
?E 十分な換気を図る。
?F 窓及び出入口には防火設備を設ける。
?G 戸には戸締りを設け、「塗料置場」「火気厳禁」等の表示を行う。
(イ) 塗料の取扱い
(a) 塗料、シンナー等、化学物質を用いて施工する場合には、労慟安全衛生、環境対応への処置を行わなければならない。
(b) 有機溶剤中覇予防について
有機溶剤を使用して作業する場合の労働者の健康障害を防止するための措置については、労働安全衛生法、有機溶剤中誨予防規則等で、作業主任者の選任や取扱い上の注意事項等の掲示等が定められている。
?@ 有機溶剤作業主任者を選任しなければならない作業場所は、有機溶剤中毒予防規則第1条に次のように定められている。
1)船舶の内部
2)車両の内部
3)タンクの内部
4)ピットの内部
5)坑の内部
6)ずい道の内部
7)暗きょ又はマンホールの内部
8)箱桁の内部
9)ダクトの内部
10)水管の内部
11)屋内作業場及び前各号に掲げる場所のほか、通風が不十分な場所
「通風が不十分な場所」とは、天井、床及び周壁の総表面積に対する窓その他の直接外気に向かって解放しうる開口部の面積の比率が3%以下の屋内作業場をいう。
通風が不十分な船舶の内部及び車両の内部については上記同様に取り扱う。
?A 有機溶剤作業主任者の職務は、有機溶剤中毒予防規則第19条の2に次のように定められている。
事業者は、有機溶剤作業主任者に次の事項を行わせなければならない。
1) 作業に従事する労働者が、有機溶剤により汚染され又はこれを吸入しないように、作業の方法を決定し、労働者を指揮すること。
2) 局所排気装置、プッシュプル型換気装置又は全体換気装置を1箇月を超えない期間ごとに点検すること。
3) 保護具の使用状況を監視すること。
4) タンクの内部において有機溶剤業務に労働者が従事するときは、第26条各号に定める措置が講じられていることを確認すること。
(c) 安全データシート(SDS)
塗料は、複数の化学物質から構成されており、その有害物による労働者の労働災害を防止したり環境への影響を考慮して、製造業者はSDS (Safety Data Sheet:安全データシート)の交付を労働安全衛生法等で義務付けられている。
その内容には、次のようなことが記載されており、施工に当たっては、これらを十分に確認し、安全・衛生対策を講じて作業を進めるとともに、廃棄物の取扱いにおいても、(g)に示すような廃棄上の注意事項に基づき処理しなければならない。
1) 安全データシートを作業場所の見やすい場所に常時掲示し、又は備え付けるなどの方法により、労働者の利用に供すること。
2) 安全データシートを活用して、安全衛生教育を行うこと。
3) 安全データシートを確認して、化学物質に関わる労働災害を防止するために必要な処置を講ずること。
4) 廃棄物処理に際して安全データシートの「廃棄上の注意」に基づいた処理を行うこと。
5) 安全データシート「環境影響情報」等に基づき、第三者等への現境管理を行うこと。
6) 安全衛生委貝会において、取り扱う化学物質の有害性、その他の性質について関係者の理解を深めるとともに、その適切な取扱い方法について調査を行うこと。
(d) 製造物責任法(PL法)への対応
製造業者は、取扱い説明書、技術資料、警告ラベル、安全データシート(SDS)等を完備し、「製造物責任法(PL法)」(平成6年法律第85号)に基づいて対応し、施工業者への情報提供を徹底し、施工業者はこれら情報に従った作業及び廃棄物処理等をしなければならない。
(e) 化学品の分類および表示に関する世界調和システム(GHS)
?@ 職場で化学物質を取り扱う際に、その危険性又は有害性、適切な取扱方法等を知らなかったことによる爆発、中毒等の労働災害が発生している。このような労働災害を未然に防止するには、その化学物質の危険性又は有害性の情報が確実に伝達され、伝達を得た事業場は、その情報を活用して適切な化学物質管理を推進することが重要である。
国際的には、平成15年に引火性や発がん性等の危険有害性の各項目にかかわる分類を行い、その分類に基づいて絵表示や注意喚起語等を含むラベル及び安全データシート(SDS)を作成・交付することなどを内容とする「化学品の分類および表示に関する世界調和システム(GHS)」が、国際連合から勧告として公表された。このGHS国連勧告を踏まえ、表示・文書交付制度を改普した改正労働安全衛生法が、平成18年12月1日に施行された。容器にはGHSに対応するラベル表示をして、文書としてはGHSに対応する情報を含む安全データシート(SDS)を提供しなければならない。
国内では平成23年まで、MSDS(化学物質等安全データシート)と呼ばれていたが、国際整合の観点からGHSで定義されているSDSに統一された。
(参考GHS : Globally Harmonized System of Classification and Labelling of Chemicals)
?A GHSに対応するラベルの例を図18.1.4に示す。ラベルには、「製品の名称」、「注意喚起語」、「絵表示(標章)」、「危険有害性情報」、「注意書き」、「供給者の特定」の情報が盛り込まれる。これらの概要を次に示す。
1) 「製品の名称」は、該当品の名称が記載される。
「成分」は、表示義務対象物質に該当するものが記載される。
2) 「注意喚起語」は、GHS付属書3又はJIS Z 7253 (GHSに基づく化学品の危険有害性情報の伝達方法 - ラベル、作業場内の表示及び安全データシート(SDS))附属書Aに割り当てられた「注意喚起語」の欄に示されている文言(「危険」又は「警告」)が記載される。
なお、危険有害性クラス及び危険有害性区分等が決定されない場合は、注意喚起語の記載を要しない。
3) 「絵表示(標章)」は、GHS付属書3又はJIS Z 7253附属書Aに割り当てられた「絵表示」の欄に記載されている標章が記載される。
なお、危険有害性クラス及び危険有害性区分等が決定されない場合は、絵表示(標章)の記載を要しない。
4) 「危険有害性情報」は、GHS付属書3又はJIS Z 7253付属書Aに割り当てられた「危険有害性情報」の欄に示されている文言が記載される。なお、危険有害性クラス及び危険有害性区分等が決定されない場合は、記載を要しない。
5) 「注意書き」は、貯蔵又は取扱い上の注意等が記載される。
6) 「供給者の特定」は、表示する者の氏名(法人の場合は法人名)、住所及び地話番号等が記載される。
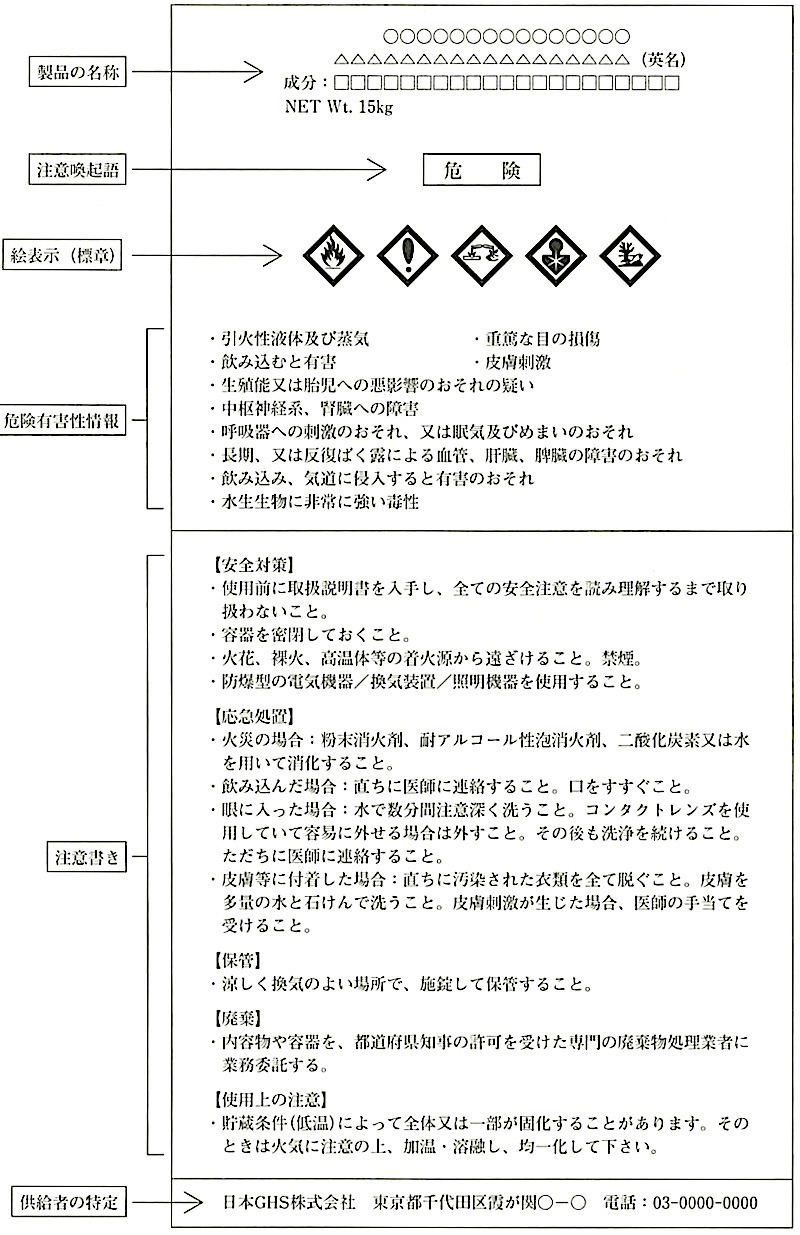
図18.1.4 GHSに基づくラベル表示の例
(f)化学物質に関するリスクアセスメント実施義務化への対応
労働者の安全を確保するため、化学物質の管理が非営に重要な事項である。 2012年、胆管がんが発症した事例が相次いだことから、2014年6月、労働安全衛生法が改正され、SDSが交付義務の対象となっている化学物質についてリスクアセスメント実施が義務付けられることとなり、2016年6月1日に施行された。
1) リスクアセスメント実施が義務付けられるのは、塗料を扱う全ての事業者である。
2) 化学物質を取り扱う際に生じるおそれのある負傷・疾病の重駕度と発生の可能性を調査し、労働災害が発生するリスクの大きさを評価するものである。
(g) 廃棄物処理への対応
塗料をはじめ各種の産業廃棄物は、「廃棄物の処理及び清掃に関する法律」(昭和45年法律第137号)等によって規制されているが、特に留意すべき事項は次のとおりである。
1) 廃棄物の減量化とリサイクルの推進
2) 廃棄物処理に関する信頼性と安全性の確保
3) 不法投棄対策等
工事に当たっては、これら法律に従って産業廃棄物を適正に処理することになるが、特に不法投棄防止のため、産業廃棄物管理票(マニフェスト)(1.3.11参照)が全ての産業廃棄物に適用されている。
したがって、産業廃棄物の発生時には、施工者が産業廃棄物の運搬又は処分の資格を有する業者との委託基準に準じて委託契約した業者に「マニフェスト」を交付し、明確な指示を与えて、処理しなければならない。
(ウ) 塗装作業への塗料の調整
(a) 希釈(粘度調整)
原則として、調合された塗料をそのまま使用する。しかし、貯蔵中に均ーな品質を保持するため施工時の条件に適した粘度より若干高い粘度の製品になっている場合、施工時の素地の状態により粘度を下げる必要がある場合、気温が低い場合等には、所定のシンナーや水等により希釈し塗装に適した状態に粘度を調整することができる。
(b) こし分け
塗料は貯蔵中に分離、沈殿、皮ばり、凝集等の現象を生じている場合があり、使用直前によく混合し、均ーな状態とする。
この場合、かくはん等で再分散しない沈殿物、皮ばり、凝集等は、必要に応じてこし分けする。これらの操作が不十分な場合には、塗装後の膜厚に色の分離や光沢低下等の欠陥を生じる場合がある。
(2) 塗装工法
(ア) 研 磨
塗装面を研磨する目的は、次に示すとおりであり、目的に応じた施工をする。なお、研磨紙等は、JIS R 6251(研磨布)及びJIS R 6252 (研磨紙)による。
?@ 下地表面に付着している汚れ等を除去し、付着性向上のために行う場合で、鉄鋼面、亜鉛めっき鋼面の塗装によく用いられる。鋳止めを工場で塗装し、現場に搬入後、次の工程を塗装する場合等に行う研磨がこれに当たる。この場合、塗装された下塗りの塗膜厚を減少させないように行う必要がある。
?A パテ処理面等を平滑にし、仕上げの平滑度を上げる場合に用いるもので、パテを厚付けした場合には、先に粗目の研磨紙で荒研ぎし、次に細かい目の研磨紙で目的の平滑度を得る。
(イ)パテの塗付け工法
被塗物の不陸、凹凸、穴等を処理して塗装仕上げの精度を高めるために用いる工法で、素地面に直接施工する場合と、各工程間に行う場合がある。
パテは、硬化後研磨を行うため、厚塗りを行う必要がある。このためひび割れが 生じないように、顔料や充槙材の配合が多くなっている。また、一般の塗料と比べて塗膜性能の向上を期待するものではないため、塗付け量は必要最小限とする。
パテ処理の工法には、パテかい、パテしごき、パテ付けの3種類がある。
?@ パテかい
局部的にパテ処理するもので、素地とパテ面との肌違いが仕上げに影響するため、注意しなければならない。
?A パテしごき
素地とパテ面との肌がそろう程度に平滑になるようパテを残し、過剰なパテをしごき取る。
?B パテ付け
パテで全面を平滑にするもので、特に美装性を要求される仕上げの場合に行う。パテが厚塗りされるため、耐久性能を要求される仕上げの場合は不適当である。
(ウ)塗料の塗装工法
(a) はけ塗り
はけの毛間に塗料をよく含ませて、はけ目を均ーに塗り広げる伝統的な塗装手段である。
はけ塗りの特徴は、はけの材質、形状、寸法等を、塗料の種類、素地の種類、被塗物の形状等に応じて選択して用いることによって、いかなる素地や部位においても、均ーな塗膜厚さに仕上げることができる。
はけ塗りのチェックポイントは、次のとおりである。
1) 指定の塗料に適合した毛の種類、長さ、形状を用いているか。
2) はけは、よく洗浄され、ぬけ毛の生じないものを用いているか。
3) はけ塗りは、むらきり、はけ目通し等の操作をしながら、均ーに塗装しているか。
4) 仕上り面に、だれ、すけ、むら等が生じておらず、均ーに塗られているか。
(b) 吹付け塗り
吹付け塗りは、塗料を霧化状態にして被抱物に吹きむらのないように吹き付け、均ーな塗膜を形成する。
吹付け塗りは、エアスプレ一方式とエアレススプレ一方式がある。
?@ エアスプレ一方式
塗料を圧縮空気によって霧化させながら、その空気圧力でスプレーガンにより吹付け塗装する方法である。適用できる塗料の種類に限界があり、高い粘度では均ーに霧化せず、低粘度に希釈するため一般的に膜厚は薄い。また、塗装時の飛散が多く風の影響を受けやすいなどの欠点がある。
エアスプレ一方式の場合のチェックポイントは、次のとおりである。
1) 塗装開始前に周辺部分は十分に養生されており、また、適切な施工条件となっているか。
2) 塗料が所定の粘度に調整されているか。
3) スプレー塗装時の所定空気圧力に設定されているか。
4) 塗装作業の被塗物とスプレーガンとの距離が一定に保たれているか。
5) スプレーガンの運行速度は一定であるか。
6) スプレーバターンの形状は膜厚が均ーで、だれ、すけ、むら等の発生はないか。
?A エアレススプレ一方式
塗料自体にポンプで10 ~ 20MPa程度の圧力を加え、スプレーガンのノズルチップから霧化して吹き付ける方法である。塗料自体に圧力を加えることができるため、高粘度や高濃度の塗料が塗装可能で、厚膜に仕上げられ、エアスプレ一方式に比べ飛散ロスも少なく効率的な施工ができる。
エアレススプレ一方式の場合のチェックポイントは、次のとおりである。
1) 塗料が所定の状態になっているか。
2) 塗料に適合したノズルチップが選定されているか。
3) 塗料が所定の圧力に加圧され、均ーに霧化し、スプレーパターンにテールが発生していないか。
4) 被塗物とスプレーガンとの距離及び運行速度は一定か。
5) 仕上り塗膜は厚さが均一で、だれ、すけ、むら等の発生はないか。
(c) ローラーブラシ塗り
ローラーブラシ塗りは、昭和30年代にアメリカから導入された塗装工法で、現在では、建築工事における塗装工法の主流となっている。ローラーブラシを構成しているアクリル又はポリエステル繊維等による塗料の含みがはけより多く、1回で広い面積に対して能率よく塗装できることが特徴である。隅角部、ちり回り等は、小ばけや専用ローラーを用いて均ーに塗る。
ローラーブラシ塗りのチェックポイントは、次のとおりである。
1) 塗料に適合した大きさ、毛の種類のローラーブラシを使用しているか。
2) 塗付け量に適合した毛の長さのローラーブラシを使用しているか。
3) 塗装時におけるローラーの回転は適切な速度で均ーに塗られているか。
4) 塗装作業はローラーマークをそろえて塗られているか。
5) 隅角部、ちり回り等は専用ローラー、小ばけ等で先行して塗られているか。
6) 仕上り面に、だれ、すけ、むら等が生じていないか。
(エ)各塗装工程の工程間隔時間及び最終養生時間
各塗装工程の工程間隔時間及び最終養生時間は、用いる塗料の乾燥硬化機構によって決まる。したがって、乾燥硬化の違いにより、次の工程に移る間隔時間を定める必要があり、また、最終工程には塗膜の使用可能までの時間を定める必要もある。
なお、工程間隔時間及び最終養生時間には、良好な塗膜形成と塗膜層間の付着性を得るために、塗料の種類によって次の工程に入るまでに一定時間以上必要な場合と、ある時間から定められた一定時間以内に次の工程に移らなければならない場合とがある。特に、水系塗料(水を主要な揮発成分とする塗料)では、気温が低く湿度が高いときに乾燥硬化が遅くなる。図18.1.5に示すように塗装・乾燥として最適な温度は20℃であるが、気温がそれよりも低くなるほど乾燥硬化が遅くなるため、良好な塗膜形成を確保するには、20℃施工時の標準工程間隔時問及び最終養生時間よりもそれぞれ長い時間が必要である。湿度についても高くなるほど乾燥硬化が遅くなることから、同様な注意を要する。
18.1.5 見 本
(1) 見本の作製
施工に先立ち、色彩計画によって決定された色、光沢、模様等の仕上げの状態について、見本塗板を作製する。
この場合、各工程が確認できるような工程塗りの見本とすることが望ましい。
(2) 見本の保管
設計担当者の確認を受けた標準見本は、最終検査時まで直射日光の当たらない場所で保管する必要がある。しかし、合成樹脂調合ペイント等の油変性塗膜は直接日光の当たらない場所に保管してあっても、徐々に反応が進行して色が変わるため、初期とは異なった色調になる場合もある。これらの見本については、事前に協議して合意を得て保管する。
18.1.6 施工管理
(1) 建築物の塗装は、内外装に施され、仕上げとしての美装のためだけでなく、各種劣化外力から被塗物を保陵することによって、建築物の耐久性を向上させることを目的としている。
このため、各種の素地に塗装された塗膜が所定の品質を確保できるように施工管理を行う必要がある。
塗装工事にかかわる具体的な施工管理の項目は、概ね次のとおりである。
(ア) 塗装工程
(a) 塗装前の素地の状態
(b) 使用材料
(c) 塗装方法
(d) 下塗り、中塗りの工程後の下地の状態(塗り工程の間隔時間、養生)
(イ) 塗付け量等
下塗り、中塗りの工程ごとに見本塗板との比較を行い、最終工程完了後「標仕」18.1.7により塗装面の確認を行う(18.1.7参照)。
(2) 施工時の条件
(ア) 乾燥硬化機構の種類
建設現場で用いられる塗料は、一般的に自然乾燥形塗料といわれ、その乾燥硬化機構には次の4種類がある。
?@ 揮発乾燥
塗料中の溶剤が蒸発するだけで塗膜を形成するもの。
(代表例:ラッカーエナメル)
?A 揮発酸化乾燥
塗料中の溶剤が蒸発しながら樹脂が空気中の酸素と反応することで、塗膜を形成するもの。
(代表例:合成樹脂調合ペイント、油性系さび止めペイント)
?B 分散粒子融着乾燥
水又は溶剤中に分散している樹脂粒子が、水又は溶剤が蒸発することで融着し塗膜を形成するもの。
(代表例:合成樹脂エマルションペイント、非水分散形塗料)
?C 反応硬化乾燥(重合乾燥)
塗膜形成要素である樹脂と副要素である硬化剤を混合することによって反応が起こり、塗膜を形成するもの。
(代表例:2液形エポキシ樹脂エナメル、常温乾燥形ふっ素樹脂エナメル)
(イ) 乾燥硬化の条件
塗料は含有成分を蒸発させたり、化学反応を生じさせて、乾燥硬化するため、施工時の温湿度に関する条件が重要となる。
図18.1.5は、一般的な塗装と養生に適する温湿度条件を示す。
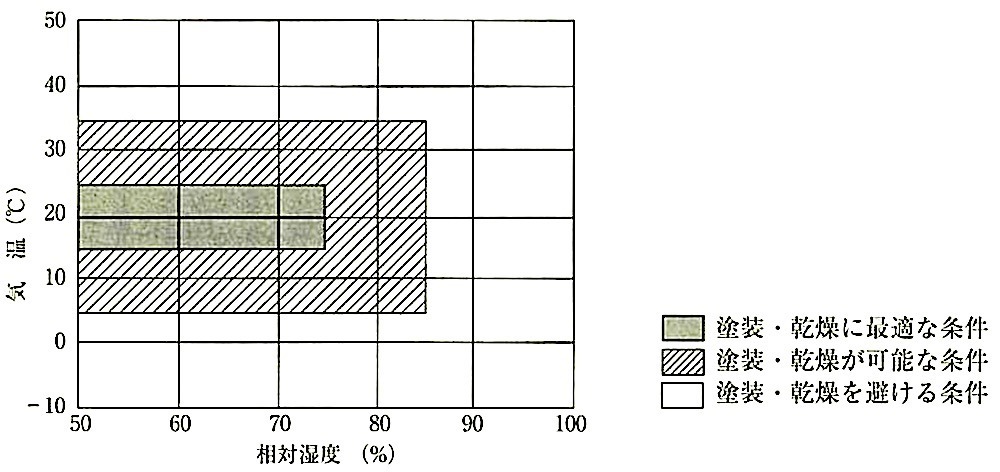
図18.1.5 塗装作業と養生に適する温湿度条件
(ウ) 養生
塗装工事における養生には、塗装しない部分に塗料が付着して汚れないようにする方法と、塗装した後の乾燥硬化過程で塗膜を正常に形成するため塗膜面に汚れが付着しないようにし、降雨、強風、直射日光等が当たるのを防いだり、温湿度を調節する方法がある。
18.1.7 塗装面の確認等
(1) 塗料及び塗膜の欠陥
塗装工事における欠陥の種類は、塗料状態における塗料の欠陥、塗装作業中における塗料の欠陥、塗装作業後における塗膜の欠陥及び塗装終了後の時間経過における塗膜の欠陥に分類でき、これらの欠陥の多くの場合は適切な予防処置を施すことにより避けることができる。これらの原因と対策を表18.1.4に示す。
(2) 塗装面の確認
塗装面の確認は、「標仕」表18.1.1による目視を標準としている。しかし、錆止め塗料塗りの場合は、塗付け量又は膜厚が防錆性能に大きく影響するため、次の方法により、これらの量又は厚さを確認することとしている。
(a) 現場における錆止め塗料塗りの場合は、膜厚測定が困難な場合が多いため、使用量から単位面積当たりの塗付け量を推定することを標準としている。
(b) 工場における鋳止め塗料塗りの場合は、電磁膜厚計等による膜厚測定の確認を標準とし、試験ロットの構成等は、施工者が品質計画で定めることとしている。
鋼製建具の工場錆止め塗装の膜厚に対する確認方法の例を以下に示す。
?@ 枠及び戸はそれぞれ別なロットとし、1組の作業班が1日に塗装した枠又は戸の全てについて、30個又はその端数を1ロットとする。
?A 1ロットから1枠又は1枚を無作為に抽出し、膜厚を以下のように測定する。
1) 枠については、縦枠2箇所(左・右)及び上枠の中央部付近各1箇所、計3箇所を1回の試験とする。
2) 戸の両面について、上段、中段及び下段の中央部付近各1箇所、計6箇所を1回の試験とする。
3) 1箇所について3点測定し、その平均値をその箇所の膜厚とする。
?B 1回の試験の平均値が、規定された膜厚以上、かつ、全ての箇所の膜厚が規定された膜厚の85%以上の場合をロットの合格とし、これ以外を不合格とする。
?C 不合格となったロットは、全てについて再塗装し、上記に準じて再度確認を行う。
表18.1.4 塗料及び塗膜の欠陥に対する原因とその対策(その1)

表18.1.4 塗料及び塗膜の欠陥に対する原因とその対策(その2)
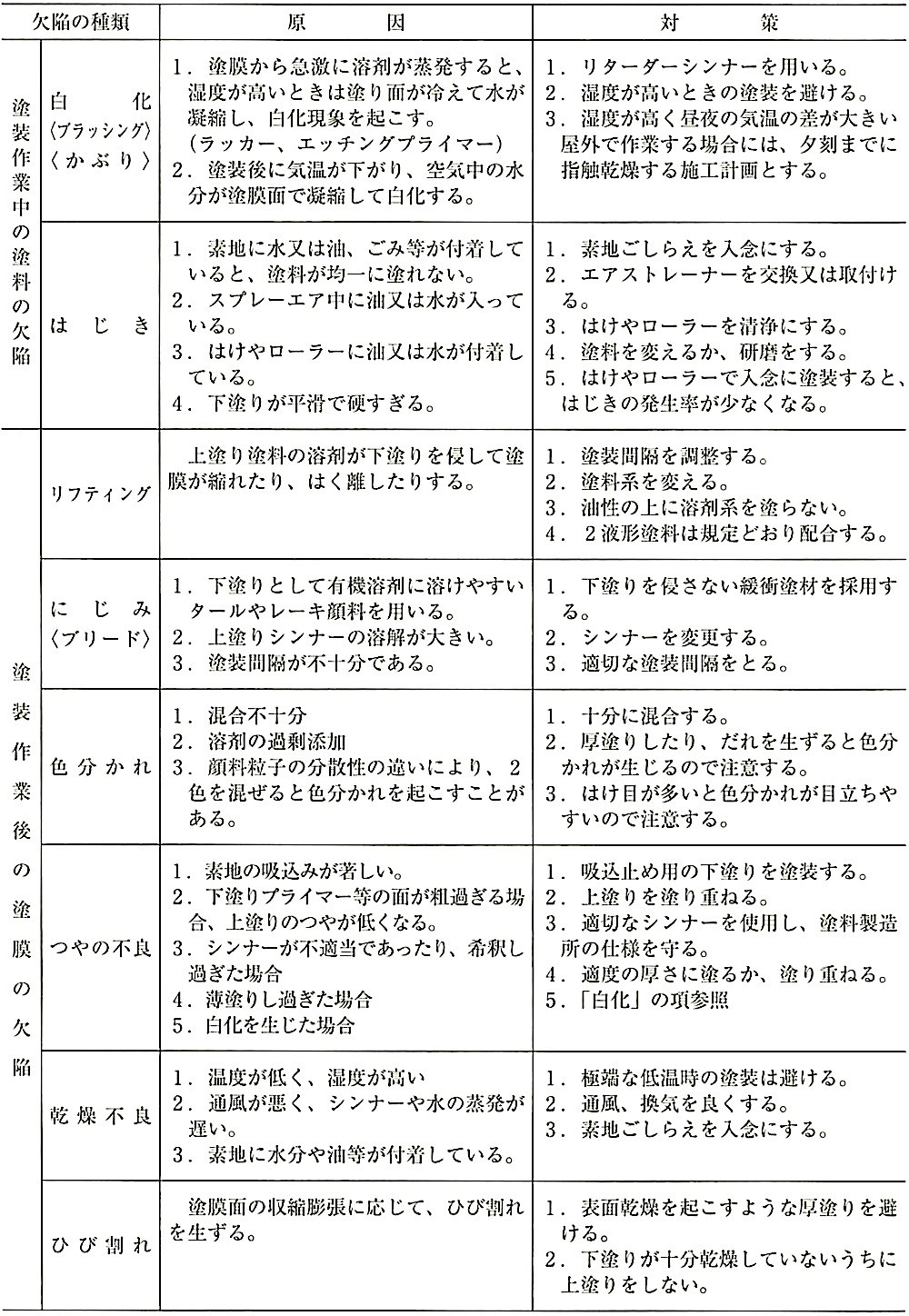
表18.1.4 塗料及び塗膜の欠陥に対する原因とその対策(その3)
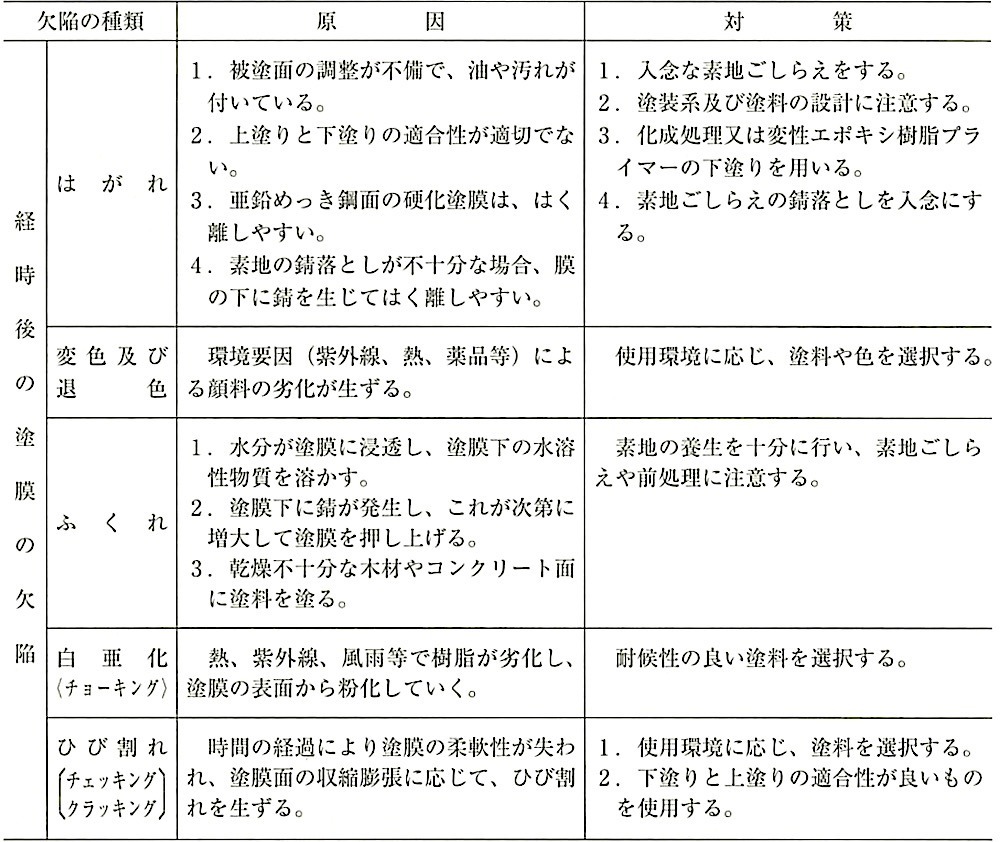